The structural design of the Roots blower muffler is based on the principles of acoustic impedance matching and energy absorption, and achieves wideband noise control through the combination of multi-stage noise reduction units. The following is a detailed analysis of its core structural principles:
---
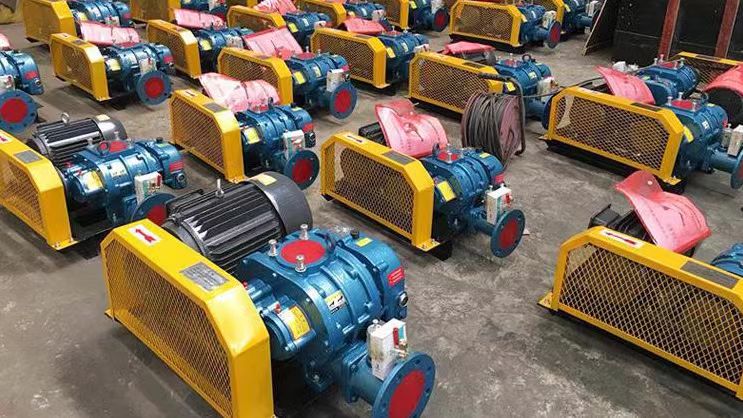
**1、 Schematic diagram of three-dimensional structure of muffler**
```plaintext
[Air inlet]
│
▼
┌───────────────────────────────────┐
│██████████████████████████████████
│█ [Expansion chamber] [Secondary resonant cavity] █│← Resistance silencing zone
│ █ ┌─────────┐ ┌───────┐ █ │
│█│ Cone shaped flow guide ││ Perforated plate │█│
│ █ └─────────┘ ├───────┤ █ │
│█│ Acoustic cotton │█│← Resistive silencing zone
│ █ └───────┘ █ │
│ ████████████████████████████████████ │
│ │
└───────────────────────────────────┘
▲
│
[Drainage valve/air outlet]
```
---
**2、 Working principle of core noise reduction unit**
**1. Resistance silencing unit (low-frequency control)**
-Expansion chamber structure:
-By suddenly expanding and contracting the cross-section (area ratio 3:1~5:1), a sudden change in acoustic impedance is generated, reflecting low-frequency sound waves of 63-500Hz.
-* * Calculation formula * *: Noise reduction amount Δ L=10lg [1+0.25 (m-1/m) 2sin2kl]
(m=expansion ratio, k=wavenumber, l=expansion chamber length)
-* * Resonant cavity structure * *:
-Side wall openings are connected to Helmholtz resonators for absorption at specific frequencies (such as 125Hz).
-* * Resonance frequency * *: f=(c/2 π) √ (σ/(V × l))
(c=sound velocity, σ=neck area, V=cavity volume, l=effective neck length)
**2. Resistive silencing unit (medium high frequency control)**
-* * Porous sound-absorbing layer * *:
-Ultra fine glass wool (fiber diameter 3-5 μ m) converts sound energy into heat energy through viscous friction.
-* * Sound absorption coefficient * *: NRC ≥ 0.85 (average at 250-4000Hz)
-* * Microperforated Plate * *:
-Plate thickness 0.8-1mm, aperture 0.3-0.8mm, forming an acoustic impedance matching layer to enhance high-frequency absorption.
---
**3、 Airflow organization design**
1. * * Diversion cone * *:
-The air inlet has a 30 ° cone angle for flow guidance, reducing turbulent regeneration noise (flow velocity decreases from 15m/s to 8m/s).
2. Maze style flow channel:
-The airflow follows an "S" - shaped path to extend contact time and improve sound absorption efficiency.
3. * * Drainage Structure * *:
-Bottom tilted at 5 °+stainless steel hydrophobic mesh to prevent the sound-absorbing cotton from becoming wet and ineffective.
---
**4、 Dynamic pressure balance design**
|* * Parameter * * | Design Value | Function|
|----------------|-------------------------|--------------------------|
|Flow area ratio | 1.3:1 (vs inlet pipe) | Control flow velocity ≤ 12m/s|
|Pressure loss compensation | guide vane inclination angle of 22 ° | reduce dynamic pressure fluctuations by ± 5|
|Temperature adaptability | -30 ℃~150 ℃ (ceramic fiber cotton) | Prevent sealing failure caused by thermal deformation|
---
**5、 Composite noise reduction performance curve**
```plaintext
Noise reduction level (dB)
▲
35│ ┌────────┐
││ Composite muffler │
30│ ┌─┘ └─┐
│ │ │
25│ ┌─┘ └─┐
││ Expansion chamber only │
20│ ┌─┘ └─┐
││ Only sound absorbing layer │
15│_______┌─┘ └─┐
│ 63 125 250 500 1k 2k 4k (Hz)
└───────────────────────────────
```
---
**6、 Special working condition adaptation plan**
1. Explosion proof type:
-Aluminum magnesium alloy shell+conductive sound-absorbing cotton (surface resistance ≤ 1 × 10 Ω).
2. * * High humidity type * *:
-Hydrophobic nano coated sound-absorbing cotton (contact angle>150 °)+electrically heated drain valve.
3. * * Ultra low frequency type * *:
-Install a 1/4 wavelength tube (customized length required for noise<63Hz).
---
**7、 Selection Calculation Example**
**Given conditions * *:
-Fan flow rate: 20m3/min
-Noise peak: 250Hz (main frequency), 500Hz (secondary frequency)
-Allowable pressure loss: ≤ 2kPa
**Silencer Design * *:
1. Expansion chamber size:
-For 250Hz, the expansion chamber length is taken as 680mm (λ/4=340/(4 × 0.25)=340mm, and the actual end correction factor needs to be considered).
2. * * Sound absorbing layer thickness * *:
-250Hz requires a sound-absorbing cotton thickness of ≥ 100mm (theoretical peak sound-absorbing thickness=λ/4).
3. * * Path Verification * *:
-Choose a DN200 muffler with an actual flow rate of 20/(π× 0.12 × 60)=10.6m/s (meets the requirements).
---
**8、 Maintain key points**
1. * * Acoustic material replacement * *:
-When the pressure loss increases by 15 or after 2 years of use (whichever comes first), the glass wool needs to be replaced.
2. * * Structural integrity check * *:
-Check the blockage rate of perforated plate holes every month (cleaning is required if it is greater than 30).
3. * * Dynamic Calibration * *:
-Every 6 months, use a sound level meter to detect noise at a distance of 1 meter. If the deviation is greater than 3dB, maintenance is required.
---
This structural design can achieve a full frequency band noise reduction of 20-35dB (A), while controlling the pressure loss within 5% of the working pressure of the fan. In practical applications, parameter tuning is required based on the frequency spectrum characteristics of the wind turbine. It is recommended to optimize the solution through CFD acoustic simulation (such as COMSOL or ANSYS Acoustics).