**Technical Guide for Selection and Application of Explosion proof Roots Blowers**
Explosion proof Roots blower is a gas conveying equipment specifically designed for flammable and explosive environments, widely used in industries such as petrochemical, coal chemical, pharmaceutical, etc. The following is a professional technical analysis of explosion-proof Roots blower.
---
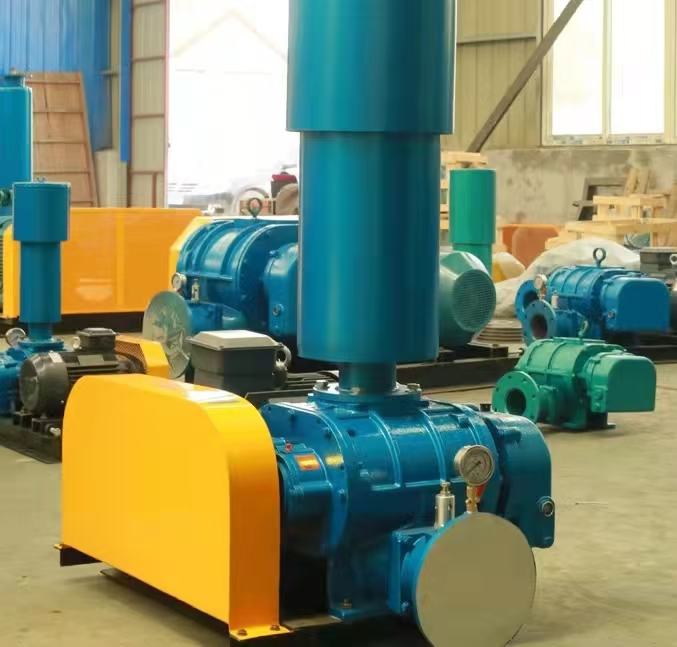
**1、 Core requirements for explosion-proof Roots blower**
**1. Explosion proof level classification**
|* * Standard * * | * * Explosion proof Mark Example * * | * * Applicable Places * *|
|----------------|-----------------------|---------------------------|
|* * Chinese Standard * * | Ex d Ⅱ B T4 Gb | Class II Grade B Gas, Temperature Group T4|
|* * Standard * * | ATEX II 2G Ex db IIB T4 | EU ATEX certification|
|* * North American Standard * * | Class I, Division 1, Group D | Petrochemical Environment|
**2. Key explosion-proof components**
-Explosion proof motor: Explosion proof type (Ex d) or increased safety type (Ex e)
-Explosion proof control box: IP65 protection, including overload protection
-Anti static treatment:
-Impeller conductive coating (surface resistance ≤ 10 Ω)
-Grounding device (grounding resistance ≤ 4 Ω)
-* * Special seal * *: Maze seal+nitrogen purge (to prevent gas leakage)
---
**2、 Selection of technical parameters**
**1. Basic parameter determination**
|* * Parameter * * | * * Calculation Method * * | * * Example Value * *|
|----------------|------------------------------|------------------------|
|Airflow | According to process requirements+10 margin | 20m3/min|
|Pressure | System resistance × 1.2 | 58.8kPa (0.6bar)|
|Medium temperature | ≤ 80 ℃ (special design required for high temperature) | Room temperature|
|Explosion proof grade | Select according to the type of explosive gas | Ex d Ⅱ B T4|
**2. Power correction factor**
-* * Gas density correction * * (when transporting light gases such as hydrogen):
\[
N = N_{air} \times \frac{ρ_{gas}}{1.29}
\]
-Elevation correction (power needs to be increased when>1000m)
---
**3、 Key points of special design**
**1. Structural explosion-proof measures**
-Shell strength: withstand 1.5 times the working pressure
-* * Gap control * *: The gap between the rotor and the housing is ≥ 0.5mm (to avoid friction sparks)
-Non sparking material: Aluminum alloy impeller (magnesium content<6)
**2. Attachment configuration**
|* * Attachment * * | * * Function * * | * * Installation Requirements * *|
|----------------|------------------------------|------------------------|
|Explosion relief film | Directional explosion relief during overpressure | Outlet pipeline|
|Oxygen content analyzer | Monitoring medium oxygen content (<5) | Inlet|
|Gas detection probe | Detecting combustible gas leakage | Within 3m around the fan|
---
**4、 Typical application scenarios**
**1. Petrochemical industry**
-Oil and gas recovery system (explosion-proof grade: Ex d Ⅱ C T1)
-Gas circulation of reaction kettle (requiring anti-corrosion design)
**2. Coal chemical industry**
-Gas pressurized transportation (dust containing gas treatment)
-Coke oven gas purification (HS corrosive environment)
**3. Pharmaceutical industry**
-Solvent vapor transportation (anti-static accumulation)
-Dust collection system (explosion-proof dust removal interlock)
---
**5、 Installation and operation specifications**
**1. Installation requirements**
-* * Distance * *: ≥ 3m from the explosion source
-Pipeline grounding: Install grounding electrodes every 6 meters
-Ventilation conditions: The installation site has a ventilation rate of ≥ 12 times/h
**2. Special precautions for maintenance**
|* * Project * * | * * Cycle * * | * * Operating Standards * *|
|----------------|------------|--------------------------------------|
|Grounding resistance detection | monthly | measured with a megohmmeter (≤ 4 Ω)|
|Explosion proof surface inspection | Quarterly | Explosion proof joint surface roughness ≤ 6.3 μ m|
|Bearing temperature monitoring | Real time | Set alarm value (shutdown at ≥ 75 ℃)|
---
**6、 Common fault handling**
|* * Fault phenomenon * * | * Explosion proof related reasons * * | * * Solution * *|
|--------------------|---------------------------|---------------------------------|
|Motor overheating | Poor heat dissipation in explosion-proof chamber | Clean the heat dissipation ribs and check the fan|
|Abnormal vibration | Accumulation of static electricity in the impeller | Check the grounding resistance and clean the impeller|
|Control box tripping | Line short circuit spark | Use explosion-proof electrician for maintenance|
---
**7、 Mainstream brands in the market**
|* * Brand Type * * | * * Represents Manufacturer * * | * * Features * *|
|-------------|------------------------|------------------------------|
|* * Brand * * | Siemens () | Full range ATEX/UL certification|
|* * Joint venture brand * * | Nanyang Explosion proof (CNE) | China's leading enterprise in explosion-proof motors|
|* * Domestic brand * * | Explosion proof series | High cost-effectiveness (Ex d Ⅱ B level)|
**Selection suggestion * *:
-Class IIC gas (such as hydrogen) must be selected as Ex d Class IIC gas
-The coal dust environment must meet both explosion-proof and dustproof requirements (Ex tD) simultaneously
-It is recommended to configure a "one in use, one backup" system, and the backup fan should have the same explosion-proof rating
If you need a specific selection plan, please provide:
① Explosive gas type ② Medium composition ③ Operating environment temperature