**Three leaf Roots blower gap adjustment method (detailed steps)**
The clearance adjustment of the three blade Roots blower is a key maintenance operation to ensure its operation, avoid rotor friction and gas leakage. Mainly adjust three types of gaps:
1. * * Mesh clearance between rotors * * (core adjustment)
2. Radial clearance between rotor and casing**
3. Axial clearance between rotor end face and wall panel**
The following are specific adjustment methods and standards:
---
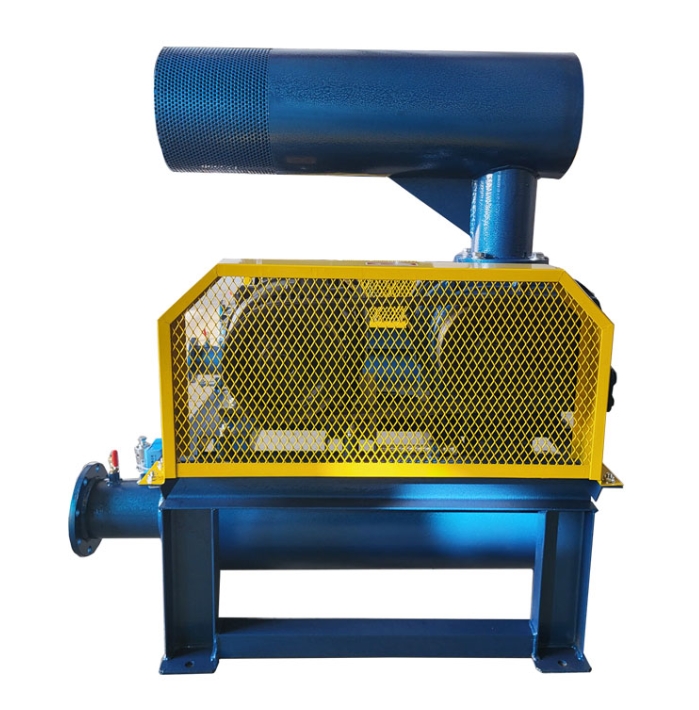
**1、 Preparation before adjustment**
**1. Tool List**
|Tool Name | Usage Description|
|----------------|----------------------------|
|* * feeler gauge * * | Measurement gap (accuracy 0.02mm)|
|* * dial gauge * * | detects axial runout and radial deviation|
|* * Copper rod/rubber hammer * * | Lightly tap the gear or bearing seat to fine tune the position|
|* * Torque wrench * * | Tighten bolts to standard torque|
|* * Marking pen * * | Mark the initial meshing position of the gear|
**2. Steps**
-* * Shutdown and power off * *, ensure locking.
-Manually rotate and confirm that the rotor can rotate freely.
-Clean the surface of the rotor and the inner wall of the casing (to avoid dust affecting the measurement).
---
**2、 Gap adjustment standard**
|* * Gap Type * * | * * Standard Range (mm) * * | * * Measuring Tool * * | * * Adjustment Method * *|
|--------------------|-------------------|-------------|---------------------------|
|* * Mesh clearance between rotors * * | 0.08~0.15 | feeler gauge | Adjust gear phase|
|* * Radial clearance * * | 0.10~0.25 | feeler gauge | Increase or decrease bearing seat gasket|
|* * Axial clearance * * | 0.20~0.40 | Dial gauge | Adjust thrust bearing or end cap gasket|
>* * Note * *: The specific values are subject to the manufacturer's manual, and the clearance should be appropriately increased for high-pressure or high-temperature conditions.
---
**3、 Detailed adjustment steps**
**1. Adjustment of meshing clearance between rotors (key steps)**
**Step 1: Position the meshing mark**
-Find the original meshing mark on the gear (such as "0" or "△") and align the marks of the two gears.
-If there is no mark, manually rotate to the 90 ° meshing position of the two rotors (one vertical, the other horizontal).
**Step 2: Measure the gap**
-Measure the gap between the two rotor working surfaces with a feeler gauge (at least 3 points: top, middle, and bottom).
-The standard value is 0.08~0.15mm and needs to be evenly distributed.
**Step 3: Adjust the gear phase**
-Loosen the gear fixing bolt (do not remove).
-* * Tap the gear lightly * * Fine adjust the angle:
-Excessive clearance → Adjust the gear clockwise.
-Gap too small → Adjust the gear counterclockwise.
-Tighten the bolt and retest the gap until it is qualified.
---
**2. Radial clearance adjustment (rotor and casing)**
**Step 1: Measure the position**
-Measure the gap between the top and bottom of the rotor and the inner wall of the casing with a feeler gauge (check multiple positions of the rotating rotor).
**Step 2: Adjustment Method**
-Control the concentricity between the rotor and the casing by increasing or decreasing the thickness of the bearing seat gasket.
-* * Standard * *: Gap of 0.10~0.25mm, deviation from top to bottom, left to right ≤ 0.05mm.
---
**3. Axial clearance adjustment (rotor end face and wall panel)**
**Step 1: Install the dial gauge**
-Place the dial gauge on the rotor shaft end and measure the axial displacement.
**Step 2: Adjust the thrust bearing**
-By increasing or decreasing the thrust bearing gasket or adjusting the thickness of the end cap gasket, the axial clearance can be controlled within 0.20-0.40mm.
---
**4、 Verified after adjustment**
1. Manual turning: Rotate several times to confirm that there is no friction or jamming.
2. * * Trial operation * *:
-Start by tapping and observe if the current and vibration are normal.
-Run without load for 30 minutes and monitor the bearing temperature (≤ 70 ℃).
---
**5、 Common problem handling**
|* * Problem * * | * * Reason * * | * * Solution * *|
|-------------------|-----------------------|--------------------------|
|* * Abnormal noise caused by rotor friction * * | The meshing clearance is too small | Adjust the gear phase again|
|* * Decreased air volume * * | Excessive radial clearance/leakage | Replace worn rotor or adjust gasket|
|* * Large axial movement * * | Wear of thrust bearing | Replace bearing or adjust gasket|
---
**6、 Precautions**
1. * * Must stop the machine for operation * *, and live adjustment is prohibited!
2. Use high-precision tools (feeler gauges, dial indicators) to reduce errors.
3. After adjusting the gears, tighten the bolts in diagonal order to avoid deviation.
4. Regularly inspect (every 6 months or 2000 hours) to prevent gaps from increasing due to wear and tear.
---
**Attachment: Schematic diagram of gap adjustment for three blade Roots blower**
```
Radial clearance (0.10~0.25mm)
↑
Inner wall of casing ← | → rotor
↓
Mesh clearance (0.08~0.15mm)
Rotor A ← | → Rotor B
```
Following the above steps can ensure the long-term stable operation of the three blade Roots blower. If it involves high-pressure or special material fans, it is recommended to have them adjusted by professionals!