**Technical Guide for Selection of Three Leaf Roots Blowers**
---
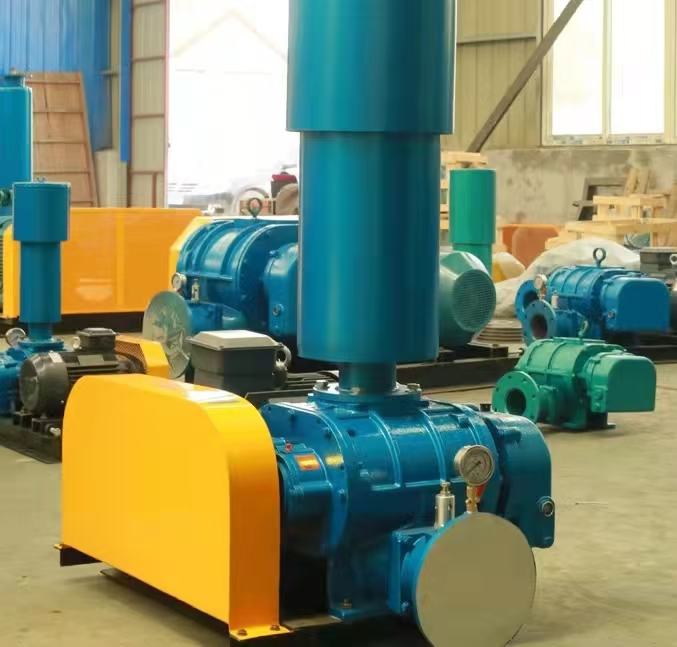
**1、 Core selection parameter matrix**
|Key Parameters | Calculation Method/Selection Basis | Typical Range|
|----------------|------------------------------------------|----------------------|
|* * Flow rate Q * * | Process requirement x 1.2 (margin factor) | 1-200m3/min|
|* * Pressure P * * | System resistance x 1.1 (including pipeline/valve losses) | 9.8-98kPa|
|Axis power N * * | \ (N=\ frac {Q × Δ P} {60 × η} \) (where η ranges from 0.65 to 0.75) | 0.75-315kW|
|* * Speed n * * | Low noise type ≤ 1450rpm, economy type ≤ 2950rpm | 980-3000rpm|
---
**2、 Analysis of adaptability to working conditions**
```mermaid
graph TD
A [medium type] -->B [clean air]
A -->C [corrosive gas]
A -->D [Flammable and Explosive Gases]
B -->E [Conventional Carbon Steel]
C -->F [316L stainless steel/FRP]
D -->G [Ex d Ⅱ CT4 explosion-proof type]
```
1. * * Temperature compensation formula * *:
$$
Q_ {Actual}=Q_ {Calibration} × \ sqrt {\ frac {273+T5 {Calibration}} {273+T5 {Real}}}
$$
(T is Celsius temperature)
2. * * Altitude correction factor * *:
|Altitude (m) | Correction factor|
|---------|---------|
| ≤1000 | 1.0 |
| 2000 | 0.83 |
| 3000 | 0.72 |
---
**3、 Example of Model Interpretation**
**Model:- 150 3L**
-* * * *: Water cooled Three Leaf Roots
-* * 150 * *: Imported caliber DN150mm
-3L: Three leaf low-speed design
**Key points of performance curve * *:
-Rated point: Q=25m3/min @ 49kPa
-Zone: 20-28m3/min (efficiency>72)
---
**4、 Transmission system selection**
|Transmission mode | Efficiency | Applicable power | Characteristics|
|------------|--------|------------|--------------------------|
|Direct connection | 98 | ≤ 55kW | Compact structure, minimal maintenance|
|Belt | 95 | 75-250kW | Adjustable speed (± 10 speed adjustment)|
|Gearbox | 92 | ≥ 280kW | Achieving Specific Speed Ratios|
**V-belt selection formula * *:
$$
P_ {Design}=K_A × P_ {Rated}
$$
(\( K_A \): Operating condition coefficient, taken as 1.3 for heavy load)
---
**5、 Special noise reduction plan**
1. Acoustic package configuration:
-Imported muffler: impedance composite type (noise reduction 25dB (A))
-Sound insulation cover: 32dB (A) insertion loss (double-layer steel plate+sound-absorbing cotton)
2. Vibration control standards:
-Basic weight ≥ 5 times the weight of the fan
-Shock absorber selection:
|Fan weight (kg) | Shock absorber stiffness (N/mm)|
|-------------|-----------------|
| 500 | 80 |
| 1000 | 150 |
---
**6、 Special working condition handling**
1. High temperature gas (≤ 250 ℃):
-Material Upgrade: Ductile Iron QT500-7
-Sealing system: graphite packing+water-cooled jacket
2. * * Granular media * *:
-Pre cyclone separator (removing particles ≥ 10 μ m)
-Impeller hardening treatment: WC Co spraying (HV ≥ 1000)
3. * * Vacuum application * *:
-Ultimate vacuum degree:- 30kPa (requires special shaft seal)
-Motor power x 1.25 (to prevent overload)
---
**7、 Energy Efficiency Optimization Strategy**
1. * * Variable frequency control * *:
-Energy saving calculation:
$$
W_ {Save}=P_N × [1- (\ frac {n1} {n0}) ^ 3] × T
$$
(\( n_1 \): Adjusted speed)
2. * * System matching * *:
-Pipeline flow rate control: 8-12m/s (DN80-DN300)
-Bend curvature radius ≥ 1.5D
---
**8、 Selection verification process**
1. * * Mechanical strength verification * *:
-Axle torque verification:
$$
τ = \frac{9550P}{n} × \frac{1}{0.2d^3} ≤ [τ]
$$
([τ]: Take 35MPa for 45 steel)
2. * * Thermal balance verification * *:
-Allow temperature rise:
|Component | Temperature|
|------------|---------|
|Bearing | 95 ℃|
|Gearbox oil temperature | 85 ℃|
---
**9、 Industry customized solutions**
|Industry | Special Configuration | Performance Focus|
|------------|-----------------------------|----------------------|
|Wastewater treatment | Anti corrosion coating (epoxy coal tar) | Continuous operation reliability|
|Pneumatic conveying | Dual oil tank lubrication system | Wear resistance life>20000 hours|
|Food and pharmaceuticals | Aseptic type (Ra ≤ 0.4 μ m) | Non polluting certification|
---
**10、 Maintain economic analysis**
1. * * Life cycle cost * *:
-Initial cost: Equipment price x 1.3 (including installation)
-Operating cost: Annual electricity fee=Power x 0.8 x 24 x 365 x Electricity price
2. Spare parts replacement cycle:
|Component | Replacement cycle | Cost proportion|
|------------|-----------|---------|
|Bearings | 2-3 years | 15|
|Seals | 1 year | 8|
|Gear | 5-8 years | 30|
---
**Note * *: For operating conditions with a flow rate greater than 100m3/min, it is recommended to use a dual machine parallel scheme (with check valves installed). After the selection is completed, FEA fluid simulation verification should be carried out (flow velocity distribution uniformity>90).