**User manual for Roots blower**
---
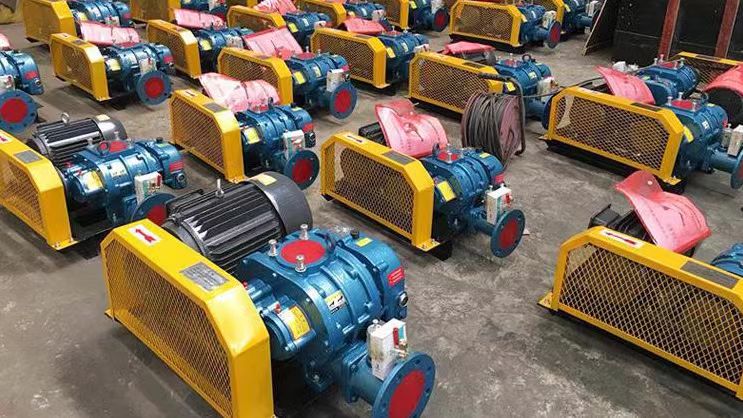
**1、 Product Overview**
Roots blower is a type of volumetric gas conveying equipment that uses two interlocked rotors to rotate inside the casing, achieving forced gas delivery. Widely used in industries such as sewage treatment, pneumatic conveying, chemical engineering, metallurgy, etc.
---
**2、 Technical parameters**
|* * Parameters * * | * * Specifications * * | * * Remarks * *|
|------------------|--------------------------|-----------------------------|
|Model | Example: RRB-150 | Fill in according to the actual model|
|Flow range | 1-500 m3/min | Customizable|
|Rated pressure | 9.8~98 kPa | Single stage/dual stage optional|
|Speed | 500~3000 rpm | Variable frequency adjustment optional|
|Motor power | 5.5~355 kW | 380V/50Hz (customizable voltage)|
|Noise | ≤ 85 dB (A) | ≤ 75 dB (A) after adding a muffler|
|Medium temperature | ≤ 80 ℃ (standard type) | High temperature type can reach 200 ℃ (water-cooled)|
---
**3、 Installation Guide**
1. * * Basic requirements**
-Concrete foundation thickness ≥ 300mm, strength C25 or above
-Pre embedded anchor bolt M20 × 400 (spacing refers to the base hole spacing)
-Use shock absorbers (recommended rubber shock absorbers, natural frequency ≤ 10Hz)
2. Pipeline connection**
-Import and export pipeline diameter ≥ fan diameter (e.g. DN150 fan with DN150 pipeline)
-The distance between the elbow and the inlet is ≥ 2 times the pipe diameter to reduce turbulence losses
-Add 3mm asbestos rubber gasket between flanges and tighten bolts diagonally
3. * * Electrical wiring**
-Motor wiring according to nameplate instructions (voltage needs to be checked for Y/△ startup)
-Grounding resistance ≤ 4 Ω
-When controlling the frequency converter, set the acceleration time to ≥ 30 seconds
---
**4、 Operation steps**
**1. Pre startup inspection**
-Confirm that the oil level is at 1/2~2/3 of the window (lubricating oil ISO VG68)
-Manually rotate the disc for 2-3 turns, and the rotor should be unobstructed
-Check the belt tension (press down with thumb to sink 10-15mm)
-The outlet valve must be fully opened** (Prohibit valve closing and starting)
**2. Start running**
1. Perform a jog test (power on for 2 seconds and immediately turn off) to confirm that the steering is consistent with the arrow on the housing
2. After starting with no load, gradually reduce the valve to the working pressure (adjustment time ≥ 1 minute)
3. Monitoring parameters:
-Bearing temperature ≤ 75 ℃
-Current ≤ rated value (e.g. 55kW motor rated current ≈ 100A)
-Vibration value ≤ 4.5 mm/s
**3. Normal shutdown**
1. First fully open the outlet valve to relieve pressure (for more than 30 seconds)
2. Cut off the power supply
3. Close the intake valve (to prevent backflow, especially for corrosive gases)
**4. Emergency stop**
Stop the machine immediately if the following situations occur:
-Bearing temperature>85 ℃
-Severe vibration or abnormal noise
-Continuous current exceeding 10
---
**5、 Maintenance and upkeep**
**1. Daily maintenance**
|* * Project * * | * * Operation * * | * * Cycle * *|
|------------------|--------------------------|----------|
|Oil level check | Add to the centerline of the oil gauge | Daily|
|Pressure/temperature recording | Record operating data | Each shift|
|Filter cleaning | Backblowing with compressed air | Weekly|
**2. Regular maintenance**
|* * Project * * | * * Operation * * | * * Cycle * *|
|------------------|--------------------------|----------|
|Lubricating oil replacement | Drain old oil, clean oil circuit | 6 months|
|Belt inspection | Replace cracked/aged belts | 12 months|
|Rotor clearance detection | feeler gauge measurement (standard 0.2~0.4mm) | 24 months|
**3. Overhaul content**
-Replace bearings and seals (recommended 8000 hours)
-Check the wear of the synchronous gear (if the backlash is greater than 0.1mm, it needs to be replaced)
-Repair of wear-resistant layer on cylinder inner wall
---
**6、 Troubleshooting**
|* * Fault phenomenon * * | * * Possible causes * * | * * Solution * *|
|----------------|---------------------|---------------------------|
|Insufficient air volume | Filter clogged/Belt slipping | Clean the filter or adjust the belt tension|
|Abnormal high temperature | Insufficient lubricating oil/cooling failure | Add oil or clean the cooler|
|Excessive vibration | Bearing damage/rotor imbalance | Replace bearings or perform dynamic balancing|
|Oil leakage | Oil seal aging | Replace mechanical seal|
---
**7、 Warning**
1. * * Strictly prohibit closing the valve and starting * *! Otherwise, it may lead to overpressure explosion of the pipe
During maintenance, it is necessary to:
-Cut off the power and hang the tag
-Evacuate pipeline pressure
3. Use copper tools in explosion-proof areas (to avoid sparks)
---
**8、 Environmental Tips**
-Waste lubricating oil needs to be professionally recycled (no dumping at will)
-Install a soundproof cover when the noise exceeds the standard (recommended noise reduction of 15dB)
---
**Attachment: After sales Service**
-Warranty period: 12 months (excluding vulnerable parts)
-Technical Support Hotline: 400-XX-XXXX
-Emergency fault response: arrive at the scene within 24 hours
(The parameters in this manual are subject to the actual product nameplate, and we reserve the right to upgrade and modify the technology)
---
**Production date: * * See body label
**Factory number: * * See nameplate