**Friction between impeller and casing of three blade Roots blower: cause analysis and solution**
When the impeller of a Roots blower rubs against the casing, it can cause abnormal noise, increased vibration, decreased efficiency, and even serious problems such as impeller damage and motor overload. The following are possible reasons and corresponding solutions:
---
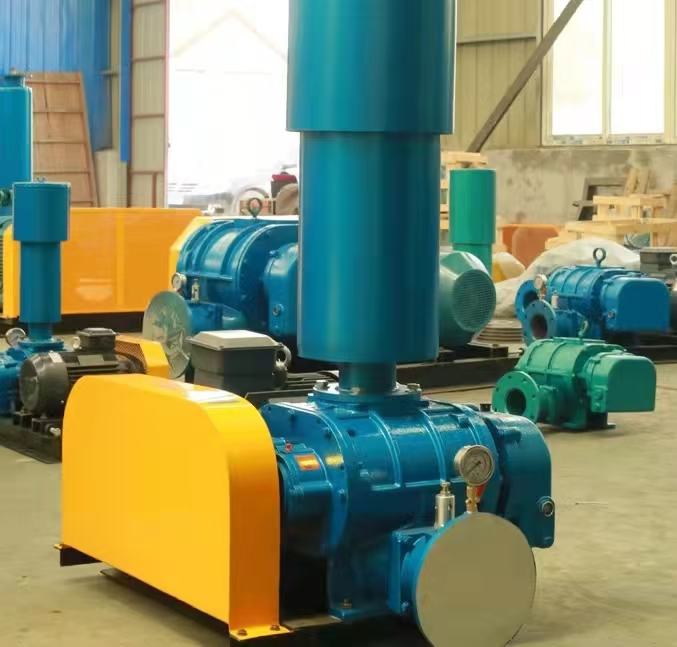
**Possible cause analysis**
**1. The clearance between the rotor (impeller) and the casing is too large or too small**
-* * Standard clearance * *: The theoretical clearance * * between the impeller and the casing of a Roots blower is generally * * 0.1~0.4mm * * (slightly different models).
-* * Gap too small * * → Direct friction produces metal scraping sound.
-The gap is too large, causing gas leakage and a decrease in air volume, but it will not cause direct friction.
**Solution * *:
-Use a * * feeler gauge * * to measure the gap and adjust it to the manufacturer's recommended value.
-If the impeller is worn, it needs to be repaired or replaced (if it is severely worn, it needs to be returned to the factory for dynamic balance correction).
---
**2. Bearing wear or damage**
-Bearing damage can cause rotor eccentricity, causing friction between the impeller and the casing.
-* * Common phenomena * *:
-Bearing abnormal noise (buzzing or metal friction sound).
-The temperature of the bearing rises (exceeding 75 ℃).
**Solution * *:
-Disassemble and inspect the bearings, replace damaged bearings (it is recommended to replace them in pairs).
-Check the lubrication system to ensure that the lubricating oil is clean and sufficient.
---
**3. Wear or misalignment of synchronous gears**
-The function of synchronous gears is to ensure the synchronous rotation of two impellers. If the gears are worn or assembled incorrectly, it can cause phase shift of the impellers and friction with the casing.
-* * Common phenomena * *:
-Abnormal noise from the gearbox.
-The impeller rotates asynchronously (visible misalignment).
**Solution * *:
-Check the gear meshing marks and recalibrate.
-If the gear is severely worn, the synchronous gear set needs to be replaced.
---
**4. Deformation or accumulation of dust and scale on the casing**
-The deformation of the casing due to heat (long-term high-temperature operation) or internal scaling (accumulation of dust and oil) may cause local gaps to become smaller, leading to friction.
-* * Common phenomena * *:
-Uneven friction sound (contact at specific locations).
-After running for a period of time, the problem worsened.
**Solution * *:
-Clean the dust and oil stains inside the casing.
-If the casing is deformed, it needs to be replaced or returned to the factory for repair.
---
**5. Rotor dynamic balance failure**
-The impeller may experience dynamic balance failure due to wear, corrosion, or foreign object impact, resulting in increased vibration during operation, which may indirectly cause friction.
-* * Common phenomena * *:
-The overall vibration of the fan exceeds the standard (can be detected by a vibration meter).
-The noise increases with the increase of speed.
**Solution * *:
-Remove the impeller and perform * * dynamic balance correction * * (requires professional equipment).
-If the impeller is severely damaged, a new impeller needs to be replaced.
---
**Repair steps (reference)**
1. * * Shutdown inspection**
-Turn off the power, exhaust the gas, and manually turn the disc to confirm the friction point.
2. * * Disassembly and Inspection**
-Check the clearance between bearings, gears, and impellers.
-Measure the vibration value (if the vibration is greater than 4.5mm/s, special attention should be paid to troubleshooting).
3. * * Targeted maintenance**
-Adjust clearance/replace bearings/repair gears/clean the casing.
4. * * Trial operation**
-Start with no load, gradually load, monitor current, noise, and vibration.
---
**Precautions**
-* * Prohibit forced operation * *, otherwise it may cause impeller breakage and motor burnout!
-* * Precise adjustment * * requires professional personnel to avoid incorrect assembly.
-After maintenance, * * airtightness testing * * and * * vibration testing * * are required to ensure normal operation.
---
**Summary**
|* * Cause of malfunction * * | * * Solution * * | * * Maintenance cost (reference) * *|
|-------------------|-----------------------------|--------------------------|
|Improper impeller clearance | Adjust or replace impeller | 500~5000 yuan|
|Bearing damage | Replace bearings (recommended to replace in pairs) | 1000~5000 yuan|
|Synchronous gear problem | Calibration or replacement of gear set | 3000~15000 yuan|
|Chassis deformation/dust accumulation | Cleaning or replacing the chassis | 2000~10000 yuan|
|Dynamic balance failure | Correction or replacement of impeller | 2000~8000 yuan|
If unable to resolve the issue on your own, it is recommended to contact * * professional repair service * * or * * original factory technical support * * to avoid further damage to the equipment!