The filter screen of the inlet muffler of Roots blower is a key component of the integrated design of noise reduction and filtration, and its structural performance directly affects the noise reduction effect and equipment life. The following is a detailed technical analysis and selection maintenance guide for filter screens:
---
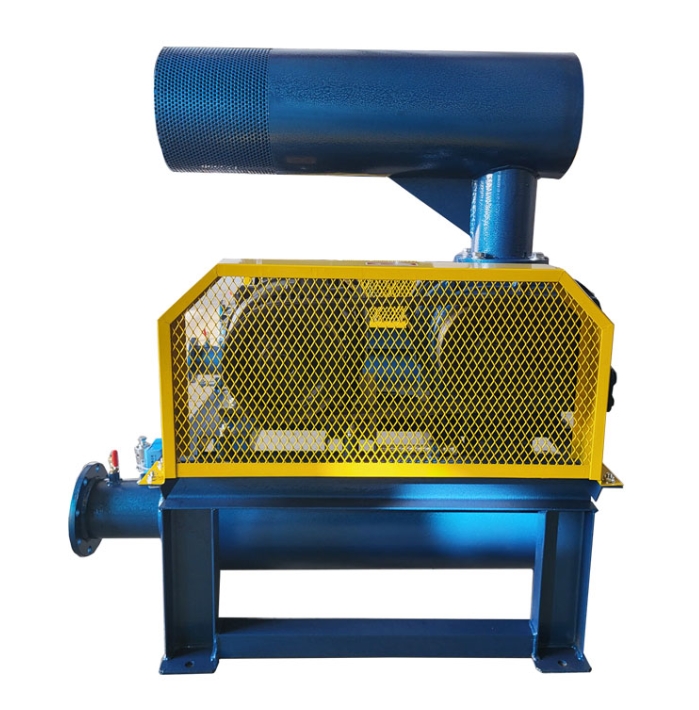
**1、 Core functions of filter screen**
1. * * Primary filtration**
-Intercept particles (dust, insects, etc.) with a diameter of ≥ 5 μ m to prevent rotor wear.
2. * * Airflow homogenization**
-The porous structure reduces intake turbulence and minimizes regeneration noise by 3-5 dB (A).
3. * * Fire protection**
-Metal material is flame-retardant to prevent sparks from entering and causing explosions (especially in biogas conditions).
---
**2、 Filter structure design**
**1. Material type**
|* * Type * * | Characteristics | Applicable Scenarios|
|----------------|-----------------------------|-----------------------|
|* * Stainless steel wire mesh * * | 304/316L, aperture 0.5-2mm | High humidity, corrosive gas|
|Galvanized punched sheet * * | Plate thickness 1-2mm, hole diameter 3-5mm | Economical, dry air|
|* * Sintered metal felt * * | Multi layer composite, filtration accuracy 1-10 μ m | Pharmaceutical and food grade requirements|
**2. Example of Composite Structure**
```plaintext
[Airflow direction]
→ ┌─────────────────┐
│ Outer layer: Stainless steel perforated plate (φ 3mm) │← Pre filtered large particles
├─────────────────┤
│ Middle layer: Stainless steel woven mesh (80 mesh) │← Fine filtration
├─────────────────┤
│ Inner layer: Silencing cotton (fiberglass) │← Sound absorption and noise reduction
└─────────────────┘
```
---
**3、 Key performance parameters**
|* * Parameter * * | Standard Value | Impact of Exceeding Standards|
|------------------|--------------------------|-------------------------|
|Filtration efficiency | ≥ 90 (5 μ m particles) | Three times increase in rotor wear rate|
|Initial pressure loss | ≤ 150Pa (at rated flow) | Fan air volume decreases by 10-15|
|Fire rating | ASTM E84 Class A | Flammable gas conditions pose a risk of explosion|
|Effective filtering area | ≥ 3 times the cross-sectional area of the intake pipe | The frequency of filter replacement is significantly increased|
---
**4、 Selection matching principle**
1. * * Aperture matching**
-General operating conditions: If the aperture is ≤ 1/3, the particle size needs to be intercepted (such as selecting a 3 μ m aperture to prevent 10 μ m particles).
2. * * Traffic adaptation**
-The flow area of the filter screen should be ≥ 1.5 times the inlet area of the fan (e.g. DN150 inlet requires ≥ 176cm2 filter area).
3. Temperature resistance requirements**
-Standard type: -30 ℃~120 ℃ (310S stainless steel should be selected for high temperature conditions, resistant to 600 ℃).
---
**5、 Special working condition design**
1. * * High humidity environment**
-Add hydrophobic coating (contact angle>150 °) and install at an inclined angle (drainage slope ≥ 10 °).
2. Flammable and explosive gases**
-Anti static treatment (surface resistance ≤ 10 Ω)+integrated spark arrester.
3. * * Food and pharmaceutical grade**
-316L stainless steel with ultrasonic cleaning process, compliant with FDA 21 CFR 177.1520.
---
**6、 Maintenance management**
**1. Cleaning cycle**
|* * Working condition * * | Cleaning interval | Method|
|------------------|------------------|----------------------|
|Clean air | 6 months | Compressed air blowback|
|Dust environment | 1 month | Soak and rinse with neutral detergent|
|High humidity | 3 months | Apply anti rust oil after drying|
**2. Replace standard**
-Pressure loss>300Pa and ineffective cleaning
-Structural damage (holes>10% of total area)
-The food industry has been using it for at least 2 years (mandatory replacement)
---
**7、 Common fault handling**
|* * Fault phenomenon * * | Cause analysis | Solution|
|------------------|-------------------|---------------------|
|Quick clogging of filter | Selection of aperture too small | Replacement of large aperture filter|
|Filter screen corroded and perforated | Material not corrosion-resistant | Upgraded to 316L stainless steel|
|Reduced noise reduction effect | Dust accumulation on the filter screen causing airflow distortion | Cleaning or replacement|
---
**8、 Comparison of mainstream suppliers**
|* * Brand * * | Features | Price (DN150 filter)|
|---------------|---------------------|------------------|
|Donaldson | Multi layer sintered metal, high precision | ¥ 1800-2500|
|Kebaite | Food grade certification, quick release design | ¥ 1200-2000|
|Domestic universal | Galvanized steel plate, economical and durable | ¥ 400-800|
---
**Operation suggestion * *:
1. Check the pressure difference on both sides of the filter screen every month (install a U-shaped differential pressure gauge);
2. Do not use wire brushes during cleaning to avoid damaging the surface oxide layer;
3. It is recommended to prepare two sets of filter screens for alternating use in chemical working conditions.
When selecting a filter, it is necessary to balance the filtration accuracy with the pressure loss cost. For critical equipment such as the semiconductor industry, it is preferred to choose the original matching filter to ensure performance matching.