The sealing device of Roots blower is a key component to prevent gas leakage, especially from the high-pressure side to the low-pressure side or external leakage. Its design and selection directly affect the efficiency, performance, and applicable medium range of the blower. The following are the types, structures, and characteristics of common sealing devices for Roots blowers:
---
**1. Main sealing types and applicable scenarios**
**(1) Labyrinth Seal**
-* * Structure * *:
A series of annular grooves between the rotor shaft and the housing form a tortuous leakage path.
-* * Features * *:
-* * Non contact * *, frictionless, long lifespan.
-Relying on small gaps (0.05~0.2mm) to block gas, the sealing effect is moderate.
-No lubrication required, suitable for clean gases such as air and nitrogen.
-* * Disadvantages * *:
When there is a high pressure difference, there is a large amount of leakage, and it needs to be used in conjunction with other seals.
-* * Application * *:
Standard models for low-pressure, non corrosive gases (such as sewage treatment aeration).
**(2) Packing Seal**
-* * Structure * *:
Fill soft materials (graphite, polytetrafluoroethylene, aramid fiber) between the shaft and the shell, and press them tightly with a cover.
-* * Features * *:
-Contact sealing requires regular adjustment of the tightness of the gland or replacement of the packing.
-Can tolerate a small amount of particulate media and has low cost.
-* * Disadvantages * *:
-Friction generates heat and requires lubrication and cooling (some designs have grease injection holes).
-High leakage rate, not suitable for toxic/flammable gases.
-* * Application * *:
In situations where low speed, low pressure, and minimal leakage are allowed (such as aquaculture oxygenation).
**(3) Mechanical Seal**
-* * Structure * *:
Composed of a moving ring (rotating with the shaft), a stationary ring (fixed), a spring, and an O-ring, the end face is precisely fitted.
-* * Features * *:
-Contact type, but with low friction coefficient and leakage rate.
-There are two types: single end face * * and double end face * *:
-Single end face: Suitable for general gases (such as biogas).
-Double end face: Introduce isolation fluid (such as glycerin) to block hazardous media (such as hydrogen sulfide and chlorine gas).
-High pressure resistance (up to 0.3MPa), corrosion resistance (materials available include silicon carbide and ceramics).
-* * Disadvantages * *:
High cost, strict installation accuracy requirements.
-* * Application * *:
The chemical and petroleum industries transport corrosive, flammable, and explosive gases.
**(4) Lip Seal skeleton oil seal**
-* * Structure * *:
The rubber or polyurethane lip contacts the shaft, and the internal spring enhances the sealing pressure.
-* * Features * *:
-Simple and compact, dust-proof and oil proof.
-Only applicable to * * low-speed, low pressure drop * * scenarios (such as bearing box oil leakage prevention).
-* * Disadvantages * *:
Easy to wear and have a short lifespan at high temperatures.
**(5) Gas Seal**
-* * Structure * *:
Similar to mechanical seals, but inert gas (such as nitrogen) is introduced between the end faces to form a gas film, achieving non-contact sealing.
-* * Features * *:
-* * Zero leakage * *, no wear and tear, extremely long lifespan.
-Requires supporting gas source and control system, cost.
-* * Application * *:
Operating conditions (such as high-purity gas transportation in the semiconductor industry).
---
**2. Key factors for selecting sealing devices**
1. * * Medium characteristics * *:
-Corrosive gases (such as chlorine gas) → * * Mechanical seal (made of Hastelloy material) * *.
-Particle dust (such as cement transportation) → * * Packing seal+labyrinth seal combination * *.
2. * * Pressure level * *:
-Low pressure (<0.05MPa) → * * labyrinth seal * *.
-Medium high pressure (>0.1MPa) → * * mechanical seal * *.
3. * * Speed and Temperature * *:
-High speed (>3000rpm) → non-contact seal (labyrinth/dry gas seal).
-High temperature (>120 ℃) → water-cooled mechanical seal or special material packing.
4. * * Requirement * *:
-Toxic/flammable gas → * * Double end mechanical seal+leakage monitoring * *.
---
**3. Typical combination of sealing systems**
-Universal type (air delivery):
**Maze seal (intake side)+skeleton oil seal (bearing side)**
-Chemical leak proof type:
**Double end mechanical seal+isolation liquid system**
-Wear resistant and dustproof type (pneumatic conveying):
**Packing seal (graphite impregnation)+labyrinth seal**
---
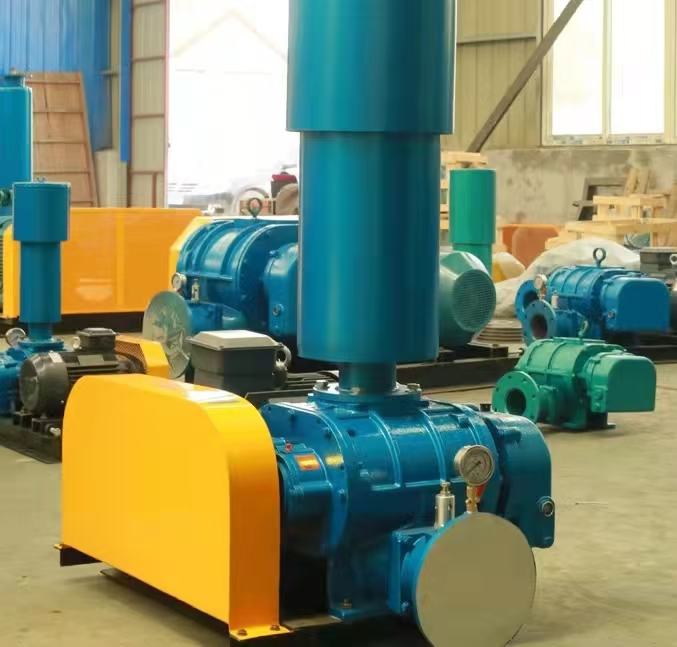
**4. Maintenance and Fault Prevention**
-* * Regular inspection * *:
-Mechanical seal: Monitor end face wear and O-ring aging.
-Packing seal: Adjust the gland bolts and add lubricating grease.
-Leakage Handling:
-Maze seal leakage increases → Check for rotor shaft runout or tooth groove wear.
-Mechanical seal leakage → Check if the cooling system is blocked or if the end face is scratched.
-Lubrication Management:
The packing seal needs to be regularly injected with lubricating grease, and the mechanical seal needs to ensure that the isolation fluid is clean.
---
**5. Special Design Case**
-Vacuum Roots Pump:
Adopting multi-stage labyrinth seal and nitrogen purging to prevent gas backflow.
-Food grade fan:
Use PTFE lip seals to prevent oil contamination of the medium.
---
**Summary**
The sealing device of Roots blower needs to be selected comprehensively based on the medium, pressure, speed, and requirements.
-Economic priority: labyrinth seal or packing seal.
-Zero leakage requirement: Mechanical seal or dry gas seal.
-* * Working condition * *: Customized combination sealing solution (such as corrosion resistance+high temperature resistance).
Proper selection and maintenance of sealing devices can significantly extend the lifespan of the machine and avoid downtime losses.