**Debugging plan for Roots blower**
The debugging of Roots blower is a key step to ensure its stable operation. Proper debugging can prevent equipment damage, improve operational efficiency, and extend service life. The following is a detailed debugging process and precautions.
---
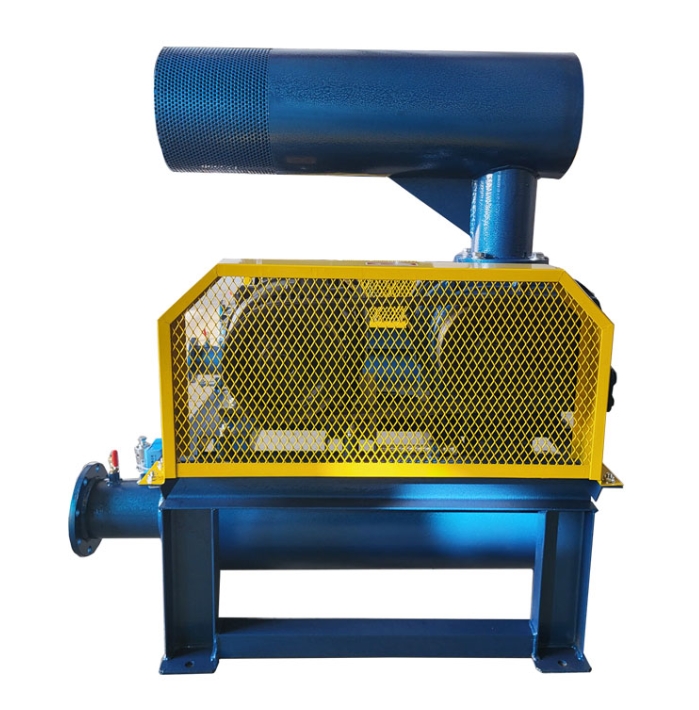
**1. Preparation work before debugging**
**(1) Check equipment and installation**
-Mechanical inspection:
-Confirm that the fan, motor, and coupling/pulley are securely installed without any looseness.
-Check if the anchor bolts are tightened and if the shock absorber pads (if any) are installed properly.
-Manually rotate and confirm that the rotor rotates smoothly without any jamming or abnormal friction noise.
-Pipeline system inspection:
-The inlet and outlet pipelines are connected correctly, the flange seal is good, and there is no leakage.
-Check if the muffler, filter, and valves (such as gate valves and check valves) are installed properly.
-Electrical inspection:
-The motor wiring is correct and the insulation resistance meets the requirements (≥ 1M Ω).
-Check if the parameter settings of the control cabinet (such as frequency converter, soft starter) are correct.
**(2) Lubrication system inspection**
-Gearbox lubricating oil:
-Check the oil level (should be at the center line of the oil gauge), the oil quality is clean and free of impurities.
-It is recommended to use manufacturer specified lubricating oil (such as ISO VG 220 gear oil) for the first operation.
-Bearing lubrication:
-Lubricated bearings require the addition of an appropriate amount of lubricating grease (such as lithium based grease).
-Oil lubricated bearings need to check if the oil circuit is unobstructed.
**(3) Device inspection**
-Pressure gauge and temperature sensor: Confirm correct installation and normal readings.
-Valve: The set pressure should be slightly higher than the rated working pressure (usually 1.1 times).
-Belt protective cover (if applicable): Ensure a secure installation to prevent accidental contact.
---
**2. No load trial operation**
**(1) Preparation before startup**
-Close the outlet valve (to avoid starting under pressure and reduce the starting current).
-Open the inlet valve to ensure smooth air intake.
-* * jog test * * (stop immediately after instantaneous start), observe whether the steering is correct (usually counterclockwise from the motor end).
**(2) No load operation (5-10 minutes)**
-Start the fan and observe:
-Whether the current is stable (should not exceed the rated current of the motor).
-Is there any abnormal vibration or noise (such as metal friction, impact sound).
-Is the bearing temperature normal (temperature rise ≤ 40 ℃, ≤ 75 ℃).
-Check the lubrication system:
-Is the gearbox oil temperature normal (≤ 80 ℃).
-Is there any leakage in the oil circuit.
**(3) Gradually loading**
-Slowly open the outlet valve and observe:
-Is the pressure gauge reading steadily rising to the set value.
-Is the motor current within the allowable range.
-Run for 30 minutes and monitor various parameters (vibration, temperature, noise).
---
**3. Load running debugging**
**(1) Adjust operating parameters**
-* * Flow regulation * *:
-If using a frequency converter, adjust the frequency (Hz) to control the speed and change the flow rate.
-If using an outlet valve, adjust the opening to control the pressure (long-term throttling operation is not recommended as it affects efficiency).
-Pressure setting:
-Ensure that the working pressure is ≤ rated pressure and avoid overpressure operation.
-The valve popping pressure should be slightly higher than the working pressure (e.g. rated at 0.5bar, valve set at 0.55bar).
**(2) Monitor key data**
|* * Parameter * * | * * Normal Range * * | * * Exception Handling * *|
|----------------|--------------------------|--------------------------|
|Current | ≤ motor rated current | overload → check load or pipeline resistance|
|Export pressure | ≤ rated pressure | overpressure → check valve and system resistance|
|Bearing temperature | ≤ 75 ℃ | Too high → Check lubrication or alignment condition|
|Vibration value | ≤ 4.5mm/s (ISO 10816 standard) | Excessive → Check the balance of the foundation bolts or rotor|
**(3) Stability testing during operation**
-* * Continuously run for 2-4 hours * *, record data:
-Pressure, flow rate, current, temperature, vibration.
-Confirm that there are no abnormal noises or leaks.
---
**4. Inspection after debugging completion**
**(1) Re inspection of fasteners**
-Check if the anchor bolts, coupling bolts, and pipeline flanges are loose.
**(2) Lubrication system maintenance**
-After the first 50 hours of operation, replace the gear oil (metal debris during the break in period).
-Add bearing grease (if applicable).
**(3) System acceptance**
-Confirm that the fan meets the design flow and pressure requirements.
-Fill out the debugging report and record all parameters.
---
**5. Common problems and solutions**
|* * Problem * * | * * Possible Cause * * | * * Solution * *|
|-------------------|--------------------------|--------------------------|
|High starting current | Outlet valve not closed, rotor stuck | Close valve, manual turning inspection|
|Unstable pressure | Pipeline leakage, valve failure | Leak detection, valve replacement|
|Abnormal vibration/noise | Poor alignment, damaged bearings | Re align and replace bearings|
|High temperature | Poor lubrication, insufficient cooling | Change oil, check cooling system|
---
**6. Precautions**
-* * Strictly prohibit starting under pressure * *: The outlet valve must be closed before starting!
-* * Avoid long-term overload operation * *: Prevent motor burnout or rotor deformation.
-* * Regular inspection * *: Check the oil level, temperature, and vibration during each shift during the initial operation.
---
**Summary**
The debugging of Roots blower should strictly follow the steps of * * no-load → light load → full load * *, with a focus on parameters such as * * pressure, current, temperature, vibration * *, etc. Proper debugging can ensure the long-term stable operation of the equipment and reduce the failure rate. After debugging is completed, regular maintenance (such as changing oil and tightening bolts) should be carried out to extend the service life.