If the two blade Roots blower cannot be manually turned (cannot be turned), it may be caused by various reasons and needs to be gradually investigated. The following are common reasons and solutions:
---
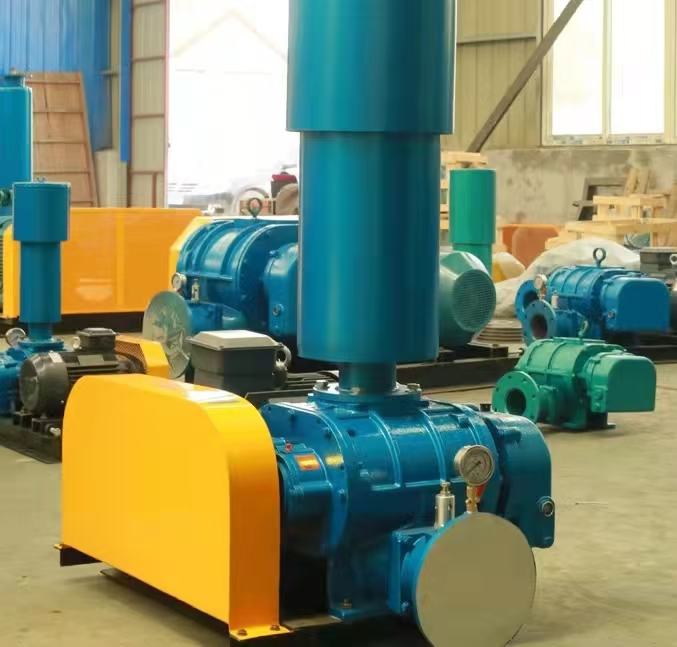
**1. Mechanical jamming (the most common cause)**
**Possible reasons * *:
-Friction between rotor and shell: Insufficient installation clearance or bearing wear can cause the rotor to collide with the shell.
-Foreign objects entering the machine cavity: particles, bolts, etc. jamming the rotor.
-Gear damage: Gear tooth breakage or misalignment causes the rotor to be unable to rotate synchronously.
-Bearing damage: Bearing jamming or lubrication failure.
**Solution * *:
1. * * Check the rotor clearance * *:
-Measure the gap between the rotor and the housing with a feeler gauge (standard value * * 0.15~0.25mm * *). If it is too small, it needs to be readjusted.
-If the rotor deforms (such as during transportation collision), it needs to be returned to the factory for repair or replacement.
2. * * Cleaning foreign objects * *:
-Open the inlet and outlet flanges and check for foreign objects (such as welding slag and tool residue) inside the machine cavity.
3. * * Check the gear * *:
-Open the gearbox cover and confirm that the gear meshing is normal, without broken teeth or misalignment (the two blade fan needs to ensure a phase difference of * * 90 ° *).
4. * * Replace bearings * *:
-Manually try to rotate the bearing. If it gets stuck, replace it (refer to the nameplate for the bearing model).
---
**2. Poor lubrication**
**Possible reasons * *:
-Gearbox oil shortage or deterioration of oil quality (such as emulsification, excessive impurities).
-Dry or contaminated bearing grease.
**Solution * *:
1. * * Change gear oil * *:
-Drain the old oil and add new oil (ISO VG 220 gear oil to the centerline of the oil window).
2. * * Add lubricating grease * *:
-Add high-temperature lubricating grease (such as molybdenum disulfide grease) to the bearings and maintain them every 3 months.
---
**3. Installation issues**
**Possible reasons * *:
-The coupling/pulley wheel is defective, causing the shaft system to get stuck under stress.
-The anchor bolts were not tightened, causing rotor friction due to fan displacement.
**Solution * *:
1. * * Re center * *:
-Direct connection type: calibrate the coupling with a dial gauge (radial/axial deviation ≤ 0.05mm).
-Belt type: Adjust the parallelism of the pulley (deviation ≤ 1mm).
2. * * Tighten the foundation bolts * *:
-Tighten gradually in diagonal order to ensure that the fan is level (error ≤ 0.2mm/m).
---
**4. Long term shutdown rusting**
**Possible reasons * *:
-The rotor or bearing may rust and adhere due to a humid environment.
**Solution * *:
1. * * Rust removal treatment * *:
-Disassemble the fan, soak the corroded area in kerosene or rust remover, and manually turn it until it becomes loose.
2. * * Rust prevention measures * *:
-When the shutdown exceeds one month, manual turning should be carried out regularly (once a week), and anti rust grease should be applied to the bearings.
---
**5. Motor issue (misjudgment)**
**Possible phenomenon * *:
-The motor did not detach from the coupling/belt, mistakenly thinking that the fan was stuck.
**Solution * *:
1. * * Disconnect the power end * *:
-Remove the coupling or belt and test separately whether the fan can be manually rotated.
---
**Emergency handling steps**
1. Power off hanging: Ensure that the equipment is powered off and hang warning signs.
2. * * Reverse micro movement * *: Try to rotate the rotor slightly in reverse, which may loosen the stuck point (do not forcefully rotate!).
3. * * Gradual disassembly * *: If it still does not rotate, it needs to be disassembled and inspected in order (first the gearbox, then the rotor cavity).
---
**Preventive measures**
-* * Regular maintenance * *: Check the rotor clearance and gear oil condition every 3 months.
-* * Inlet filtration * *: Install a ≤ 10 μ m filter to prevent foreign objects from entering.
-* * Avoid overpressure * *: The operating pressure should not exceed the nameplate calibration value (two blade fans are more sensitive to overpressure).
---
**Summary**
The two blade Roots fan disk not moving is often due to mechanical jamming or lubrication failure, and requires systematic investigation. If it is difficult to handle on your own, it is recommended to contact the manufacturer or professional maintenance personnel to avoid violent disassembly that may cause secondary damage.