The working principle of the two blade Roots blower is based on volumetric gas delivery, which achieves forced gas delivery by rotating two interlocked impellers inside the casing. The following is a detailed analysis of its core principles:
---
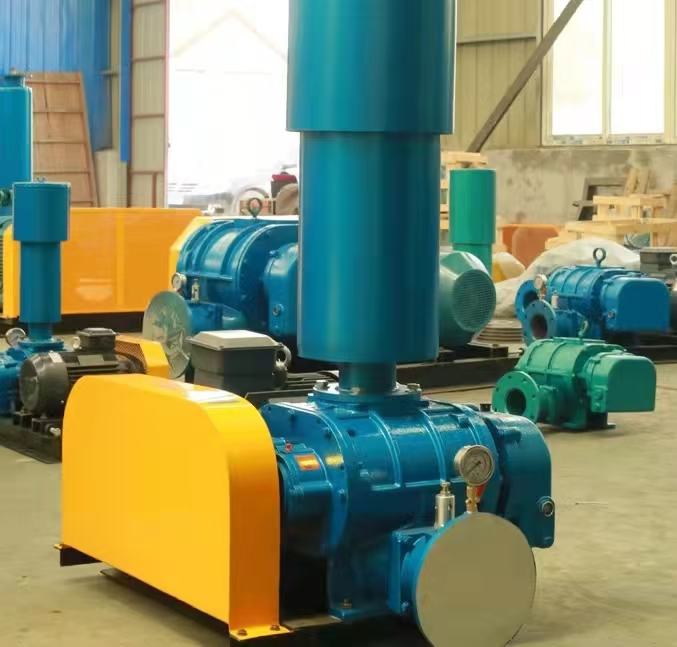
**1、 Core working principle**
1. * * Impeller meshing motion**
-Two * * two bladed impellers * * (straight or involute) maintain a * * 180 ° phase difference * * and rotate in opposite directions through synchronous gears.
-The impeller and the inner wall of the casing form a closed chamber, and gas is brought into the chamber from the inlet side and pushed to the outlet side as the impeller rotates.
2. * * Volume change process**
-* * Inhalation stage * *: When the impeller disengages, the chamber volume increases, forming negative pressure to suck in gas (Figure ①→②).
-Transport stage: The impeller rotates to seal the gas inside the chamber (Figure ② → ③).
-Exhaust stage: The impeller meshes again, the chamber volume decreases, and the gas is forcibly discharged (Figure ③ → ④).
```plaintext
[Schematic diagram of work cycle]
① Inhalation → ② Closure → ③ Push → ④ Exhaust
```
3. * * Mandatory conveying characteristics**
-The flow rate is directly proportional to the rotational speed and is almost unaffected by the outlet pressure (which is determined by the resistance of the backend system).
-Without internal compression process, sudden increase in exhaust pressure will cause * * airflow pulsation * * (muffler needs to be installed).
---
**2、 Key structural role**
|* * Component * * | * * Function * *|
|-----------------|-------------------------------------------------------------------------|
|* * Impeller * * | Two blade straight plate or involute type, with high precision requirements (clearance of 0.15~0.4mm)|
|* * Synchronous gear * * | Ensure non-contact meshing between the two impellers (backlash of 0.10~0.15mm)|
|* * Chassis * * | Cast iron/stainless steel material, inner wall needs precision machining (roughness Ra ≤ 1.6 μ m)|
|* * Bearing group * * | Bearing radial/axial force (commonly used tapered roller bearings)|
---
**3、 Performance characteristics**
1. * * Advantages**
-Flow stability: * * pulsation rate<5 * * (three leaf type<3).
-Simple structure: no valves, few friction parts, low maintenance costs.
2. * * Limitations**
-Low efficiency: * * adiabatic efficiency is about 50-65 * * (three leaf type can reach 70).
-Loud noise:** 85~95dB (A) * *, noise reduction measures are required.
---
**4、 Comparison with Three Leaf Fan**
|* * Characteristics * * | * * Two leaf type * * | * * Three leaf type * *|
|----------------|----------------------------|----------------------------|
|Pulsation | Large (strong periodicity) | Small (smoother airflow)|
|Noise | Significant high-frequency noise | Mainly mid low frequency, noise reduction of 10dB|
|Manufacturing cost | Low (simple impeller processing) | High (complex impeller profile)|
|Applicable scenarios | Low pressure extensive working conditions (such as pneumatic conveying) | Precision gas supply (such as sewage treatment)|
---
**5、 Typical Fault Principle Analysis**
1. Abnormal increase in exhaust pressure**
-Reason: Impeller wear leads to increased internal leakage and decreased volumetric efficiency.
-Judgment: The current increases but the flow rate decreases, and the impeller clearance needs to be measured.
2. * * Gear tooth breakage**
-* * Mechanism * *: Impeller asynchronous collision (excessive gear backlash or lubrication failure).
3. * * Bearing overheating**
-Cause: Unbalanced axial force (the axial force fluctuation of the two bladed type is greater than that of the three bladed type).
---
**6、 Key points of selection design**
1. * * Traffic calculation * *:
\[
Q = 4 \times V \times n \times \eta_v
\]
-(V): Impeller displacement per revolution (m3/r)
-(n): Speed (rpm)
-(\ eta-v \): Volumetric efficiency (0.75~0.85)
2. * * Pressure Limit * *:
-Two leaf type is recommended to be ≤ 78.4kPa, and three leaf type is preferred for high-pressure conditions.
---
Mastering this principle can effectively guide the use and maintenance of fans, such as:
-Avoid prolonged overpressure operation (accelerating impeller wear)
-Regularly check the gear meshing markings (to prevent phase misalignment)
-Add a filter at the inlet (dust will increase gap leakage)