**Installation and commissioning requirements for Roots blower**
The installation and commissioning of Roots blowers directly affect their operational efficiency, stability, and service life. To ensure reliable operation of the equipment, it is necessary to strictly follow the specifications for operation. The following are detailed installation and debugging requirements:
---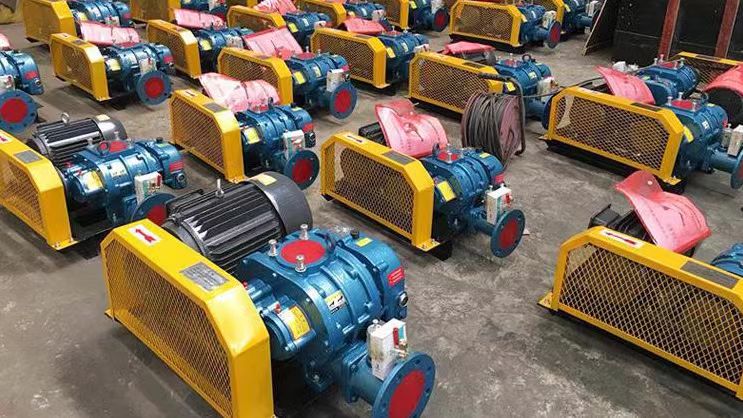
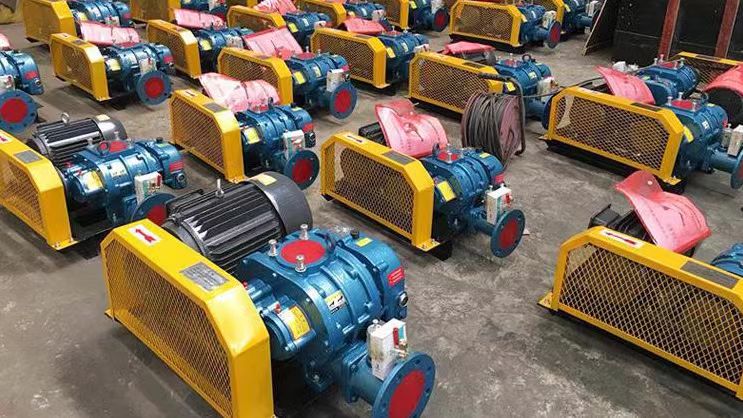
**1、 Installation requirements**
**1. Basic requirements**
-Basic strength: The concrete foundation needs to meet the requirements of equipment weight and vibration. It is recommended to reserve anchor bolt holes (for secondary grouting fixation).
-Levelness: The deviation of the basic surface levelness is ≤ 0.1mm/m to avoid uneven bearing force on the shaft due to inclination.
-* * Vibration reduction measures * * (optional):
-Install vibration damping pads (rubber or spring dampers) between the fan base and foundation.
-Use soft joints at pipeline connections to reduce vibration transmission.
**2. Fan positioning and fixation**
-* * Lifting requirements * *:
-Use specialized lifting equipment to avoid colliding with the rotor or casing.
-Maintain horizontal lifting to prevent internal parts from shifting due to tilting.
-Tightening of foundation bolts:
-Use a torque wrench to gradually tighten in diagonal order to ensure even force distribution.
-After secondary grouting and curing for at least 48 hours, fine adjustment can be carried out.
**3. Pipeline connection**
-* * Import/Export Pipeline * *:
-Pipeline diameter ≥ fan interface diameter to reduce airflow resistance.
-Avoid sharp bends (it is recommended that the curvature radius of the bend be ≥ 1.5 times the pipe diameter).
-Cleanliness:
-Clean the welding slag, iron filings and other impurities inside the pipeline before installation (to prevent them from entering the fan and damaging the rotor).
-* * Support and fixation * *:
-The pipeline needs to be independently supported to avoid direct external forces acting on the fan interface.
**4. Electrical and Control Systems**
-Motor wiring:
-Check that the voltage and frequency are consistent with the motor nameplate (e.g. 380V/50Hz).
-The cable specifications must meet the current requirements and be reliably grounded.
-* * Protective device * *:
-Install overload protection (thermal relay) and phase loss protector.
-Pressure gauge and valve (recommended to be set at 1.1 times the rated pressure).
---
**2、 Debugging requirements**
**1. Pre debugging inspection**
-* * Mechanical part * *:
-Manually turn the rotor 2-3 times to confirm that there is no jamming or abnormal noise.
-Check if the lubricating oil (grease) is sufficient (the gearbox oil level is at the centerline of the window).
-Electrical part:
-Measure the insulation resistance of the motor (≥ 1M Ω).
-Perform a jog test to confirm that the motor direction is consistent with the fan identification (reversing will damage the impeller).
**2. No load trial operation**
-* * Running time * *: 30 minutes to 1 hour.
-* * Monitoring project * *:
-Vibration: The vibration speed of the bearing part is ≤ 4.5mm/s (detected by a vibration meter).
-Temperature: Bearing temperature ≤ 70 ℃, gearbox temperature ≤ 80 ℃.
-* * Noise * *: No abnormal friction or impact sound (normal noise ≤ 85dB).
-* * Exception Handling * *:
-Immediately stop the machine and check for abnormal vibration and temperature (such as poor alignment and insufficient lubrication).
**3. Load trial operation**
-Gradually increase the voltage:
-First fully open the outlet valve, then slowly close the valve to the working pressure after starting.
-Prohibit sudden loading or overpressure operation (which may cause motor overload).
-* * Performance Verification * *:
-Check whether the flow rate and pressure have reached the design values (using flow meters and pressure gauges for testing).
-Record whether the current and voltage are stable (the current should not exceed the rated value of the motor).
**4. System integration debugging**
-* * Linkage with process equipment * *:
-If used for sewage treatment aeration, it is necessary to check the uniformity of aeration and dissolved oxygen concentration.
-Automated testing (if controlled by PLC):
-Simulate faults (such as overvoltage and overheating), verify alarm and shutdown functions.
---
**3、 Precautions**
**Prohibited items * *:
-Do not operate the fan without installing a coupling protective cover.
-Do not operate without a filter at the intake (dust can damage the rotor).
-Long term no-load operation is prohibited (which may cause gear overheating).
**Maintenance Tip * *:
-Replace the lubricating oil after the first 200 hours of operation, and replace it every 2000 hours thereafter.
-Regularly check the tension of the belt (if it is a belt drive) and the aging of the sealing components.
---
**4、 Common problems and solutions**
|* * Fault Symptoms * * | * * Possible Causes * * | * * Solutions * *|
|--------------------|-----------------------|-----------------------------|
|Vibration exceeding the standard | Poor alignment/rotor imbalance | Re alignment or dynamic balance correction|
|* * Bearing overheating * * | Insufficient lubrication/small clearance | Add lubricating grease or adjust bearing clearance|
|* * Insufficient air volume * * | Pipeline blockage/inconsistent speed | Clean the pipeline or check the motor speed|
|* * Abnormal noise * * | Gear wear/foreign objects entering | Replace gears or clean internal impurities|
---
**Summary**
The installation and commissioning of Roots blowers must strictly follow the principle of "mechanical first, electrical second, no-load first, load second", with a focus on controlling centering accuracy, gap adjustment, and system protection functions. After debugging is completed, it is recommended to sign the acceptance record and archive the operating data to provide a basis for subsequent maintenance.