**Detailed explanation of imported muffler for Roots blower**
During the operation of Roots blower, strong aerodynamic noise (usually up to 90-110dB) is generated due to the periodic exhaust and airflow pulsation of the rotor. To reduce noise pollution and meet environmental requirements (such as GB 12348 "Emission Standard for Industrial Enterprise Boundary Environmental Noise"), it is necessary to install a muffler at the air inlet. The following are the technical points and selection guidelines for imported mufflers:
---
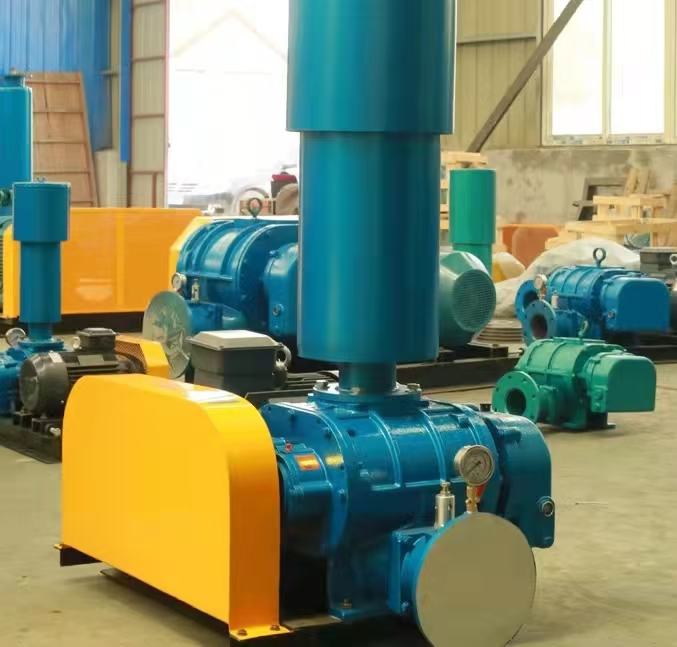
**1. The function of imported muffler**
-* * Reduce intake noise * *: Broadband noise caused by airflow turbulence and pressure pulsation (main frequency range 500~4000Hz).
-* * Protect the fan * *: Filter out large particles and impurities to prevent dust from entering and damaging the rotor (some mufflers have integrated filters).
-* * Optimize airflow * *: Reduce intake resistance and improve fan efficiency.
---
**2. Type and structure of muffler**
**(1) Resistive muffler * * (most commonly used)
-Principle: Utilizing porous sound-absorbing materials (such as glass wool and rock wool) to dissipate sound energy.
-* * Structure * *:
-Shell: Carbon steel/stainless steel cylinder.
-Lining: Perforated board wrapped with sound-absorbing material (thickness 50-100mm).
-Airflow channel: honeycomb or folded plate type, extending the sound wave absorption path.
-Noise reduction effect: 15-25dB (A), suitable for medium to high frequency noise.
**(2) Resistance muffler**
-Principle: To cancel out noise (for low-frequency noise) through sound wave reflection interference.
-* * Structure * *: Expansion chamber and resonant cavity design.
-* * Applicable scenarios * *: Low frequency noise is prominent (<500Hz) and the airflow contains oil/water vapor (resistive materials are prone to clogging).
**(3) Composite muffler**
-* * Combination design * *: Resistive+resistant structure, covering all frequency band noise (such as HXK series).
-* * Typical application * *: High pressure Roots blower (pressure>0.8bar) or strict noise requirements (such as near hospitals and schools).
---
**3. Key performance parameters**
|* * Parameter * * | * * Typical Value * * | * * Explanation * *|
|------------------|--------------------------|----------------------------------|
|* * Noise reduction volume * * | 15~30dB (A) | Select based on the noise spectrum (determined by actual measurement or simulation)|
|* * Resistance loss * * | ≤ 500Pa | Excessive resistance loss can affect fan flow and energy consumption|
|* * Applicable flow rate * * | Matching fan inlet diameter | Such as DN100, DN150, etc|
|* * Temperature resistance * * | -30 ℃~150 ℃ | Stainless steel material is required for high temperature working conditions|
---
**4. Selection steps**
1. * * Determine the characteristics of the noise source * *:
-Measure the noise spectrum of the fan inlet (with priority given to 1/3 octave band analysis).
-Clearly identify the frequency bands that require noise reduction (such as high-frequency selective impedance and low-frequency selective impedance).
2. * * Calculate the size of the muffler * *:
-The cross-sectional area of the muffler should be ≥ 1.2 times the cross-sectional area of the fan inlet (to avoid excessive airflow velocity causing regenerative noise).
-The length is usually 3-5 times the diameter (such as a DN200 muffler with a length of 600-1000mm).
3. * * Material selection * *:
-Ordinary air: Carbon steel spray coating (high cost-effectiveness).
-Corrosive gas: 304/316 stainless steel.
4. * * Additional Features * *:
-Integrated filters (such as sintered felt filter cartridges, with an accuracy of ≤ 10 μ m).
-Rainproof design (outdoor installation requires the installation of a rainproof cap).
---
**5. Installation precautions**
-* * Location * *: Try to be as close as possible to the inlet of the fan (distance ≤ 1.5 times the pipe diameter) to avoid the influence of the middle bend on the effect.
-* * Support * *: The independent bracket is fixed to prevent weight from directly acting on the fan interface.
-Sealing: Add rubber gaskets at the flange connection to prevent air leakage (air leakage will reduce the noise reduction effect).
-* * Maintenance * *:
-Check whether the sound-absorbing material is powdered every 3 months (the replacement cycle is usually 2-3 years).
-Regularly clean the filter (if the pressure difference is greater than 300Pa, it needs to be cleaned or replaced).
---
**6. Common Problems and Solutions**
|* * Problem * * | * * Reason * * | * * Solution * *|
|---------------------|-----------------------|--------------------------------|
|* * Poor noise reduction effect * * | Mismatched frequency band selection | Use a composite muffler or install secondary noise reduction|
|* * Excessive resistance * * | Blocked muffler channel | Clean the filter or replace the large diameter muffler|
|Shell vibration noise | Airflow resonance | Strengthening brackets or adding damping layers|
---
**7. Recommended brand and model**
-* * Brand * *:
-Changsheng (CSR) series resistive muffler
-* * Brand * *:
-TROX() resistant muffler (suitable for flammable gases)
---
**Summary**
The selection of imported mufflers for Roots blowers requires comprehensive consideration of factors such as noise spectrum, pressure loss, and medium characteristics. For conventional industrial applications, * * resistive silencers * * (such as ZP type) offer cost-effectiveness; If the noise frequency band is complex or contains corrosive gases, it is recommended to choose a composite or stainless steel muffler. Regular maintenance is required after installation to ensure long-term noise reduction effect.