The following are the key parameters and technical specifications for the maintenance of Roots blowers, covering the entire process of disassembly, inspection, assembly, and commissioning, for reference and execution by maintenance personnel:
---
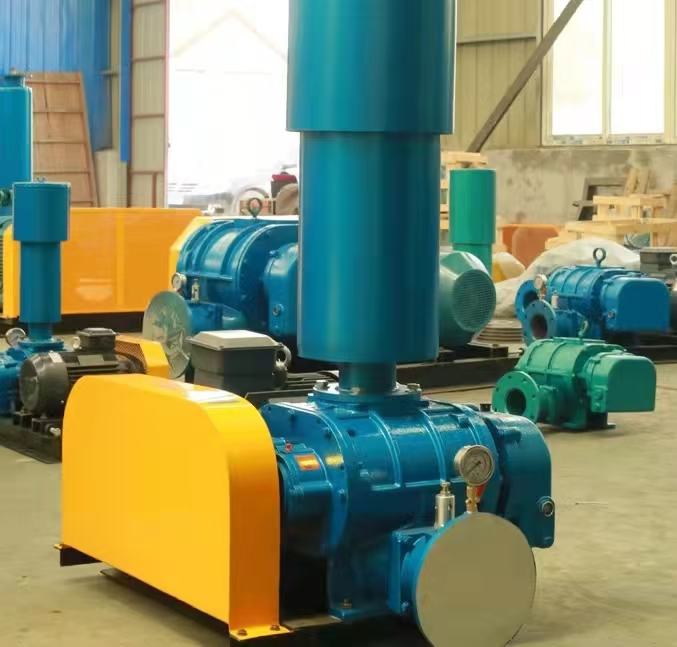
**1、 Core Maintenance Parameter Table**
|* * Maintenance Project * * | * * Standard Value * * | * * Limit Value * * | * * Testing Tool * *|
|--------------------|----------------------------|----------------------------|--------------------------|
|Radial clearance of impeller * * | 0.15~0.25 mm (new machine) | If it is greater than 0.4 mm, it needs to be replaced | feeler gauge (0.02mm accuracy)|
|Axial clearance of impeller * * | 0.10~0.20 mm |>0.3 mm needs to be adjusted | Dial gauge (axial gauge)|
|* * Gear backlash * * | 0.10~0.15 mm | If it is greater than 0.25 mm, the gear needs to be replaced | Lead wire indentation method|
|* * Bearing clearance * * | 0.03~0.05 mm (tapered roller) |>0.1 mm needs to be replaced | Micrometer+dial gauge|
|* * Coupling centering error * * | Radial<0.05 mm |>0.1 mm needs to be realigned | Laser centering instrument|
|Vibration speed * * | ≤ 4.5 mm/s (ISO 10816 standard) |>7.1 mm/s Shutdown for maintenance | Vibration analyzer|
|* * Bearing temperature * * | ≤ 75 ℃ (normal operation) |>85 ℃ Emergency stop | Infrared thermometer|
---
**2、 Key component maintenance specifications**
**1. Impeller maintenance**
-Wear and tear repair:
-Blade tip wear ≤ 1mm can be repaired by welding (using EDCrMo-A welding rod).
-Wear>2mm requires overall replacement (dynamic balance requirement G2.5 level).
-Gap adjustment:
-Adjust the axial clearance by increasing or decreasing the thickness of the bearing seat gasket.
-The radial clearance needs to be adjusted synchronously by adjusting the positions of the two impellers (maintaining parallelism ≤ 0.02mm).
**2. Gear maintenance**
-Tooth surface inspection:
-If the pitting area is less than 5, it can be polished and continue to be used.
-Broken teeth or peeling>3mm2 must be replaced.
-* * Mesh marking * *:
-During assembly, it is necessary to ensure that the contact spot is ≥ 60 tooth height and ≥ 50 tooth length.
**3. Bearing replacement**
-* * Disassembly method * *:
-Use a hydraulic wheel puller (tension ≤ 80% of the bearing's ultimate load).
-Heating temperature ≤ 120 ℃ (avoid annealing).
-Installation torque (taking SKF 22220 bearing as an example):
-Tightening nut torque: 450~500 N · m.
-Lubricating grease filling amount: 1/3~1/2 of the bearing chamber volume.
---
**3、 Sealing system maintenance**
|Sealing type * * | * * Replacement standard * * | * * Installation points * *|
|---------------|----------------------------|----------------------------------|
|* * Skeleton oil seal * * | Lip cracking or hardening | Apply lubricating grease to avoid reverse installation|
|Maze seal * * | Gap>0.3 mm | Adjust to 0.1~0.2 mm|
|* * Mechanical seal * * | Leakage rate>5 mL/h | The roughness of the static ring end face should be Ra ≤ 0.2 μ m|
---
**4、 Performance verification after maintenance**
1. * * No load test * * (30 minutes):
-Current fluctuation ≤ ± 5 rated value.
-Abnormal noise detection: Use a listening stick to detect abnormal noise in gears/bearings.
2. * * Load Test * * (2 hours):
-The air volume deviation is less than ± 3 (compared with the nameplate).
-Pressure fluctuations are less than ± 2.
---
**5、 Guidelines for Handling Common Malfunctions**
|* * Fault Symptoms * * | * * Possible Causes * * | * * Maintenance Measures * *|
|---------------|----------------------------|----------------------------------|
|Insufficient air volume | Excessive impeller clearance/Belt slippage | Adjust clearance to 0.2mm/Tensioning belt|
|Excessive vibration | Bearing damage/impeller imbalance | Replace bearings/perform dynamic balancing (residual amount ≤ 1g)|
|High temperature | Poor lubrication/Overpressure operation | Replace lubricating oil (ISO VG220)/Check system resistance|
---
**6、 List of Maintenance Tools**
1. * * Essential Tools * *:
-Hydraulic wheel puller (10~50 tons), torque wrench (100~600N · m), laser alignment instrument.
2. * * Consumables * *:
-Sealing glue (temperature resistance above 200 ℃), molybdenum disulfide grease, cleaning agent (residue free type).
---
**Note * *: After repair, a repair record must be filled out, including the replacement part model, clearance adjustment value, test data, etc. It is recommended to perform preventive maintenance every 5000 hours to reduce the sudden failure rate by over 60%.