The structural design of the outlet muffler of Roots blower directly affects the noise reduction effect and system resistance. The following is a detailed structural analysis and design points of a typical muffler:
---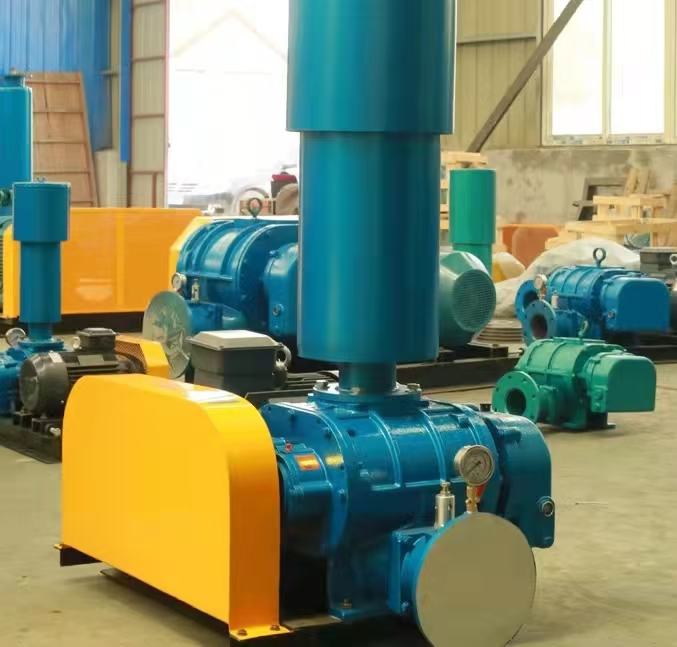
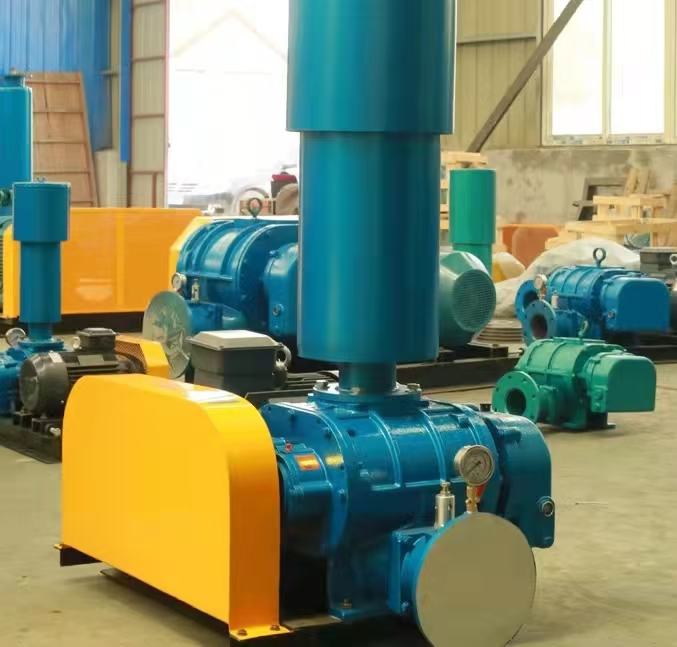
**1、 Core structure composition**
**1. Shell**
-Material: Carbon steel (Q235B) or stainless steel (304/316L), with a thickness of 2-6mm (depending on the pressure rating).
-* * Shape * *: cylindrical (mainstream) or square (customized), with flanges at both ends (PN10/PN16 standard).
-* * Anti corrosion treatment * *: Spraying or lining aluminum foil glass wool (corrosive gas environment).
**2. Silencing unit**
-* * Acoustic layer**
-* * Acoustic material * *: Ultra fine glass wool (density 48-64kg/m3) or rock wool (temperature resistance>300 ℃).
-* * Protective layer * *: perforated plate (galvanized steel plate, aperture diameter of 3~8mm, perforation rate of 20~30).
-* * Airflow channel**
-Expansion chamber type: Reflecting sound waves through a sudden change in cross-section (suitable for low-frequency noise).
-Maze style: Multiple baffles extend the airflow path (noise reduction can reach 25-35dB (A)).
**3. Drainage structure**
-* * Bottom water collection tank * *: equipped with DN20 drainage valve (for treating condensation water of humid and hot gases).
-* * Tilt design * *: The shell is tilted 5 °~10 ° to promote drainage (optional).
**4. Connecting components**
-Import and export flanges: ANSI 150 or DIN standard, equipped with rubber gaskets.
-* * Lifting ear/bracket * *: The load-bearing capacity is ≥ 1.5 times the weight of the muffler (shock absorbers need to be added under vibration conditions).
---
**2、 Silencing principle**
1. * * Resistive noise reduction**
-Sound absorbing materials consume sound energy (for medium and high frequency noise above 500Hz).
2. * * Resistance silencing**
-Expansion chamber/resonant cavity cancels out specific frequency noise (for low frequencies of 63-500Hz).
3. * * Composite noise reduction**
-Combining resistive and resistant structures (broadband noise reduction, typical frequency range 50~4000Hz).
---
**3、 Key design parameters**
|* * Parameter * * | * * Typical Value * * | * * Impact * *|
|------------------|----------------------------|----------------------------|
|Silencing volume | 15~30dB (A) | measured at a distance of 1m from the device|
|Pressure loss | < 2kPa (at rated flow) | Excessive pressure loss will reduce the efficiency of the fan|
|Airflow velocity | 10~20m/s | > 25m/s is prone to generating regenerative noise|
|Working temperature | -20 ℃~120 ℃ (standard type) | High temperature requires heat-resistant fiber cotton|
---
**4、 Special structural variation**
1. Explosion proof type**
-The shell is thickened to 8mm, and the sound-absorbing layer is made of anti-static rock wool (Ex d Ⅱ BT4 certified).
2. * * Anti corrosion type**
-Full stainless steel shell+PTFE coated sound-absorbing cotton (suitable for chlorine gas, hydrogen sulfide, etc.).
3. * * Low resistance type**
-Honeycomb airflow channel (pressure loss<1kPa, sacrificing 10-15 damping volumes).
---
**5、 Selection and matching key points**
1. * * Traffic matching**
-Silencer diameter ≥ fan outlet diameter (e.g. fan outlet DN150, choose DN150~DN200 silencer).
2. * * Frequency adaptation**
-Tested fan noise spectrum (if 125Hz is the main frequency, the resistance structure needs to be strengthened).
3. * * Installation method**
-Vertical installation requires an internal water accumulation guide plate (to avoid the failure of sound-absorbing cotton due to soaking).
---
**6、 Maintenance precautions**
1. * * Regular inspection**
-Clean the dust on the surface of the sound-absorbing cotton every 3 months (compressed air blowback).
2. * * Drainage management**
-Manual drainage is required every week in humid and hot environments (automatic drain valves need to be checked monthly).
3. * * Damage repair**
-If the area of corrosion on the perforated plate exceeds 30, it needs to be replaced (otherwise, the noise will rebound).
---
**7、 Industry standard reference**
-* * Noise test * *: GB/T 1236-2017 (equivalent to ISO 5801)
-Fire Protection Requirements: GB 8624-2012 (Class A Combustion Performance of Acoustic Materials)
-Pressure vessels: GB/T 150-2011 (Calculation basis for shell strength)
---
**8、 Typical fault handling**
|* * Fault phenomenon * * | * * Cause analysis * * | * * Solution * *|
|------------------|----------------------------|----------------------------|
|Reduced noise reduction effect | Blockage of sound-absorbing cotton/blockage of perforated panels | Replacement of sound-absorbing materials|
|Abnormal vibration | Internal baffle detachment/bracket loosening | Welding reinforcement+dynamic balance correction|
|Sudden increase in pressure loss | Freezing of condensate/blockage of foreign matter | Heating and tracing or shutdown cleaning|
---
**9、 Design differences among mainstream manufacturers**
-* * Domestic muffler * *: focuses on cost control (such as using ordinary glass wool with a noise reduction of about 20dB).
-Imported brand (e.g.):
-Modular design (replaceable silencing unit);
-Pressure loss optimization (patented diversion structure, Δ P<1kPa).
---
**Conclusion: The structural design of a Roots blower muffler needs to balance three major elements: noise reduction performance, airflow resistance, and durability. When selecting, parameters such as flow rate, pressure, and noise spectrum of the fan should be provided, and priority should be given to selecting the muffler model that matches the original fan. For special working conditions such as high temperature and corrosion, it is recommended to customize the design.