The pressure drop of Roots blower may be caused by various reasons, and it needs to be gradually investigated from the aspects of * * gas source system, mechanical components, operating parameters * *, etc. The following is a detailed analysis of the reasons and solutions:
---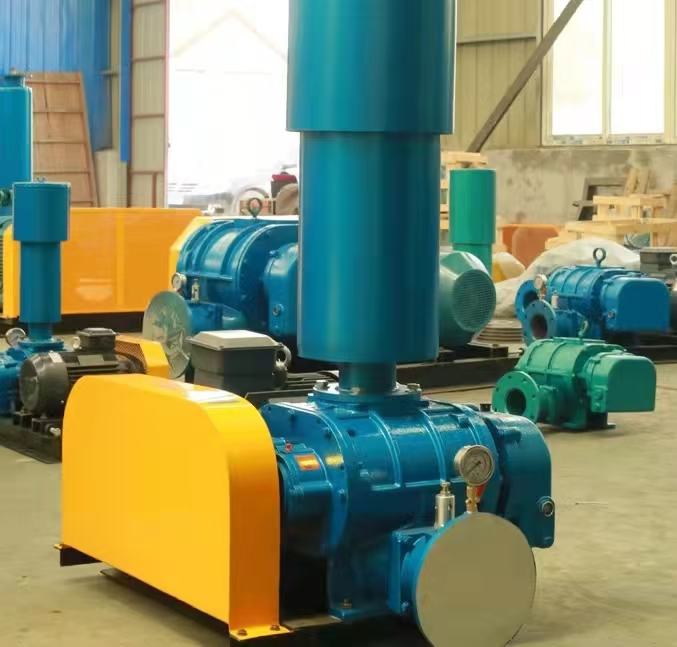
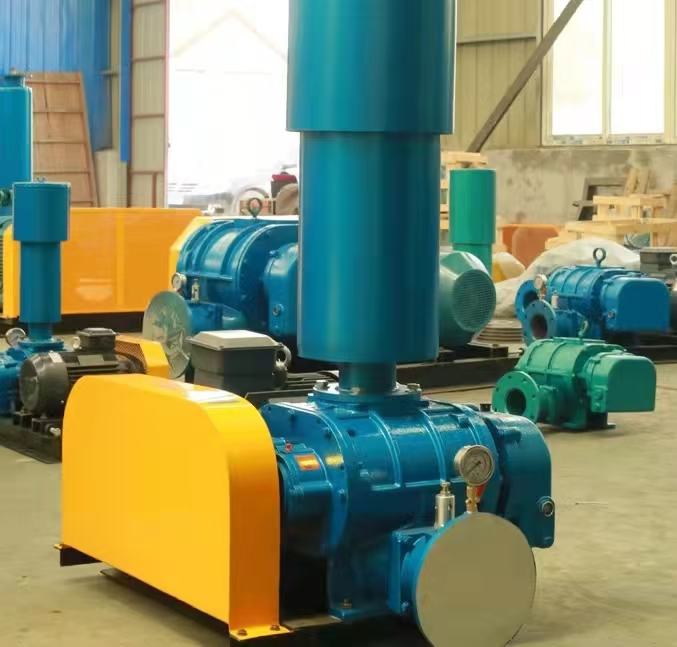
**1、 Air source system issues**
1. * * The intake filter is clogged**
-Phenomenon: The fan current decreases and the suction noise weakens.
-Reason: The accumulation of dust in the filter element leads to an increase in intake resistance and a decrease in air volume.
-Solution: Clean or replace the filter element (recommended to check monthly).
2. Pipeline leakage or valve not fully opened**
-Phenomenon: Pressure gauge fluctuates and there is a hissing sound of air leakage in the pipeline.
-Reason: Aging flange gasket, insufficient valve opening, or pipeline rupture.
-* * Resolve * *:
-Use soapy water to detect leaks and tighten them.
-Confirm that the valve (especially the outlet valve) is fully open.
3. * * Medium change**
-Phenomenon: The pressure decreases but the air volume is normal.
-Reason: Changes in gas density during transportation (such as temperature and humidity increase).
-Solution: Adjust process parameters or recalculate system resistance.
---
**2、 Mechanical component failure**
1. Impeller wear or increased clearance**
-Phenomenon: Increased fan noise accompanied by metal friction sound.
-* * Reason * *:
-Dust entering causes impeller wear (commonly seen in steel mills and cement plants).
-After long-term operation, natural wear occurs and the clearance exceeds the standard value of 0.2~0.4mm.
-* * Resolve * *:
-Measure the clearance with a dial gauge, adjust the gasket or replace the impeller (in pairs).
2. * * Synchronous gear wear**
-Phenomenon: Abnormal noise from the gearbox and significant pressure fluctuations.
-Reason: Poor gear meshing (backlash>0.15mm).
-Solution: Replace the gear and calibrate the backlash (standard 0.08~0.12mm).
3. * * Bearing damage**
-Phenomenon: Increased body vibration and bearing temperature>90 ℃.
-Reason: Insufficient lubrication or excessive load leading to increased bearing clearance.
-Solution: Replace the bearings (recommended SKF/NSK brand) and check the lubrication system.
4. Belt slippage (belt drive type)**
-Phenomenon: The belt creaks and the speed decreases.
-Reason: The belt is aging or the tension is insufficient.
-Solution: Adjust the tensioner or replace the belt (preferably with a sag of 5-10mm).
---
**3、 Abnormal running parameters**
1. * * Speed decrease**
-* * Reason * *:
-The motor voltage is unstable (such as phase loss).
-Inverter setting error (frequency reduction).
-Solution: Check the power supply voltage and calibrate the output frequency of the frequency converter.
2. * * System resistance reduction**
-* * Reason * *:
-The demand for downstream gas equipment has decreased (such as reduced blockage of aeration discs).
-Unexpected expansion of pipeline cross-sectional area (such as pipeline damage).
-Solution: Check the status of the gas end equipment and repair the pipeline.
---
**4、 Other reasons**
1. * * Valve misoperation**
-Phenomenon: Sudden drop in pressure, valve exhausts.
-Reason: The set pressure is too low or the valve core is stuck.
-Solution: Reset the valve pressure (usually 1.1 times the rated pressure).
2. Lubricating oil deterioration**
-Phenomenon: The gearbox temperature rises and the noise becomes dull.
-Reason: Excessive emulsification or impurities in the lubricating oil lead to increased friction.
-Solution: Replace ISO VG220 gear oil (every 2000 hours or 6 months).
---
**5、 Troubleshooting process**
1. * * Preliminary examination * *:
-Listen to abnormal noises, touch vibrations, check pressure gauges and current values.
2. * * System troubleshooting * *:
-Check the filter → pipeline → valve → gas equipment.
3. * * Mechanical disassembly inspection * *:
-If there are no issues mentioned above, the impeller, gears, and bearings need to be disassembled and inspected.
---
**6、 Preventive measures**
-* * Regular maintenance * *:
-Clean the filter element monthly and check the seals quarterly.
-Calibrate the impeller clearance and gear meshing annually.
-* * Operation monitoring * *:
-Install pressure sensors and vibration probes for real-time monitoring.
---
**Summary**
The root causes of pressure reduction in Roots blowers are mostly four types of problems: leakage, blockage, grinding, and sliding. Quick positioning method:
1. First, check the external components (pipes, filter cartridges).
2. Re measure the interior (clearance, gear).
3. Calibration parameters (speed, voltage).
If you are unable to solve the problem on your own, it is recommended to contact the manufacturer to provide * * performance curve chart * * for further analysis by comparing it with actual operating data!