**Explosion proof Roots blower suitable for full gas analysis**
---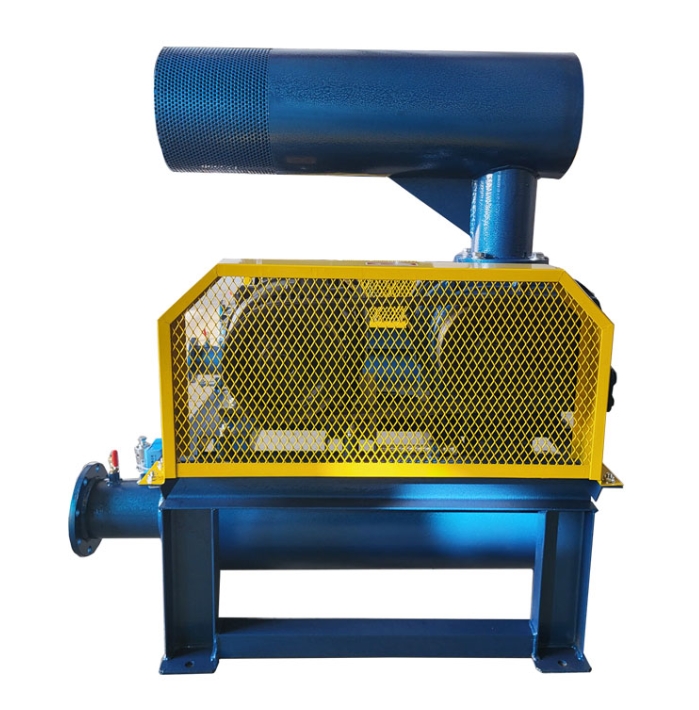
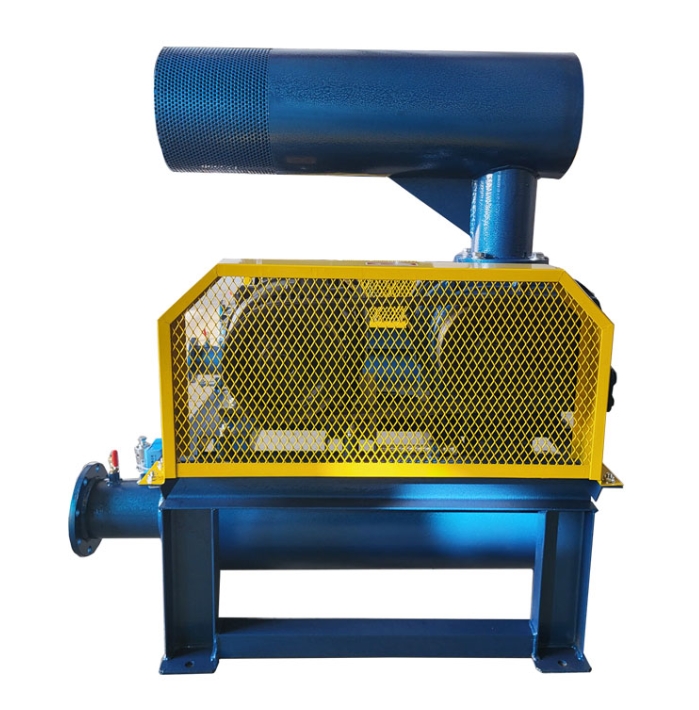
**1、 Classification standard for explosive gases**
According to * * IEC 60079-0 * * and * * GB 3836.1 * *, the applicable gases for explosion-proof Roots blowers are divided into three categories based on * * test gap (MESG) * * and * * ignition current ratio (MICR) * *:
|* * Gas Group * * | * * Representative Gas * * | * MESG (mm) * * | * * MICR * * | * * Applicable Explosion proof Grade * *|
|--------------|-----------------------------|--------------|----------|----------------|
|* * IIA * * | Propane, methane, gasoline vapor |>0.9 |>0.8 | Ex d IIA|
|* * IIB * * | Ethylene, coke oven gas | 0.5~0.9 | 0.45~0.8 | Ex d IIB|
|* * IIC * * | Hydrogen, acetylene, carbon disulfide |<0.5 |<0.45 | Ex d IIC ()|
---
**2、 Typical Applicable Gas List**
**1. Common industrial gases**
|Gas type | Explosion limit (vol) | Temperature group | Explosion proof requirements|
|----------------|----------------|----------|--------------------------|
|Methane * * | 5-15 | T1 | Ex d Ⅱ A T1 (coal mine requires Class I)|
|Hydrogen * * | 4-75 | T1 | Ex d Ⅱ C T1 (strict level)|
|* * Propane * * | 2.1-9.5 | T1 | Ex d Ⅱ A T1|
|Ethylene * * | 2.7-36 | T2 | Ex d Ⅱ B T2|
|Ammonia gas * * | 15-28 | T1 | Ex d Ⅱ A T1 (requires corrosion resistance)|
**2. Special working condition gas**
|Gas | Special Requirements | Recommended Fan Materials|
|-----------------|-------------------------------------|---------------------|
|Hydrogen sulfide * * | NACE MR0175 certification required (HS partial pressure ≥ 0.0003MPa) | 316L stainless steel+Hastelloy alloy|
|Chlorine gas * * | Requires PTFE lining (highly corrosive) | Fully lined with fluorine structure|
|Oil and gas mixture * * | Electrostatic protection (surface resistance<10 Ω) | Carbon steel coating+conductive coating|
---
**3、 Not applicable for gas types**
1. * * Strong oxidizing gas**
-Oxygen (O) concentration>23.5
-Undiluted state of chlorine gas (Cl)
2. * * Spontaneous combustion gas**
-Silane (SiH, self ignition temperature<50 ℃)
-Phosphine (PH)
3. * * Highly toxic gases**
-Phosgene (COCl)
-Hydrogen cyanide (HCN)
>* * Note * *: The above gases require non-contact fans such as positive pressure ventilation or magnetic levitation
---
**4、 Key points of selection technology**
1. * * Temperature group matching**
-Gas ignition temperature vs equipment surface temperature:
```math
Gas>Equipment+50 ℃ (Yudu)
```
*Example: The ignition temperature of ether is 160 ℃, and T3 group (≤ 200 ℃) equipment needs to be selected*
2. * * Special structural requirements**
-* * Hydrogen working condition * *:
-The shaft seal needs to use dual mechanical seals
-Impeller dynamic balance level G1.6 (conventional G2.5)
-Acetylene working condition:
-Prohibit the use of copper alloy components (to avoid the generation of explosive acetylene copper)
-Gap between shell joint surfaces ≤ 0.1mm
3. * * System Integration Specification**
-Gas concentration monitoring interlock must be configured (LEL ≥ 20 alarm, ≥ 40 shutdown)
-Pipeline system * * Static grounding resistance * * ≤ 10 Ω
---
**5、 Industry application cases**
|Industry | Typical Gas | Explosion proof Configuration | Additional Measures|
|----------------|----------------------|----------------------------------|-------------------------|
|* * Petrochemical refining * * | Propylene, benzene vapor | Ex d Ⅱ B T3+ATEX certification | Nitrogen purging system|
|* * Biogas Engineering * * | Methane+Hydrogen Sulfide | Ex d Ⅱ A T1+HS Protection | Pre installation of Wet Gas Cabinet|
|* * Pharmaceutical Fermentation * * | Ethanol Vapor | Ex d Ⅱ A T2+Aseptic Design | Explosion proof Variable Frequency Control|
|Coal Chemical Industry * * | Water Gas (CO+H) | Ex d Ⅱ C T1+CO Monitoring | Explosion Relief Disc (0.15MPa)|
---
**6、 Maintain standards**
1. * * Pre maintenance treatment**
-Replace nitrogen until O<2
-Combustible gas detection<10LEL
2. * * Explosion proof component replacement**
-Must use * * original factory explosion-proof certified parts**
-After repairing the joint surface, it is necessary to retest the gap (Class IIC tolerance ± 0.01mm)
3. * * Operation monitoring**
-Continuous monitoring of bearing temperature (≥ 85 ℃ alarm)
-Monthly vibration testing (speed value ≤ 4.5mm/s)
---
**7、 Interpretation of Certification Mark**
-* * Certification * *:
 when selecting, in order to carry out additional protective designs such as corrosion and particulate matter.