**Analysis and Solution of the Necessity of Dust Prevention for Roots Blowers Used in Boilers**
---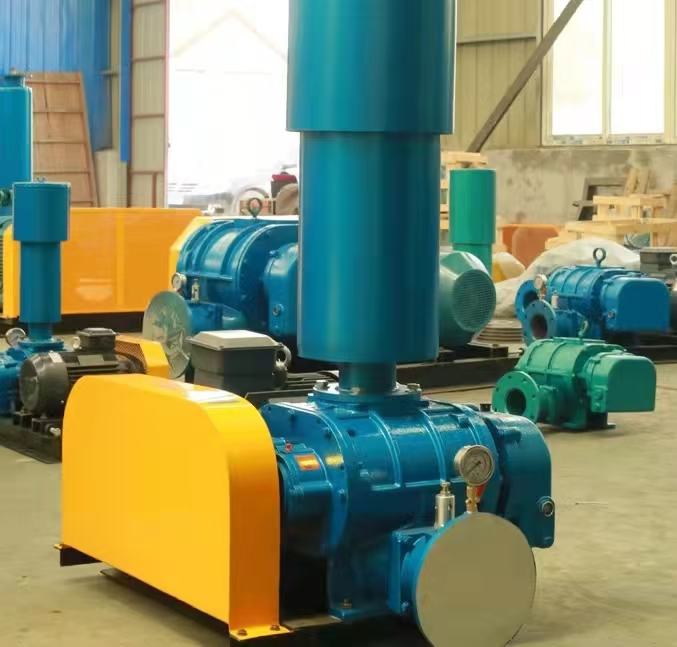
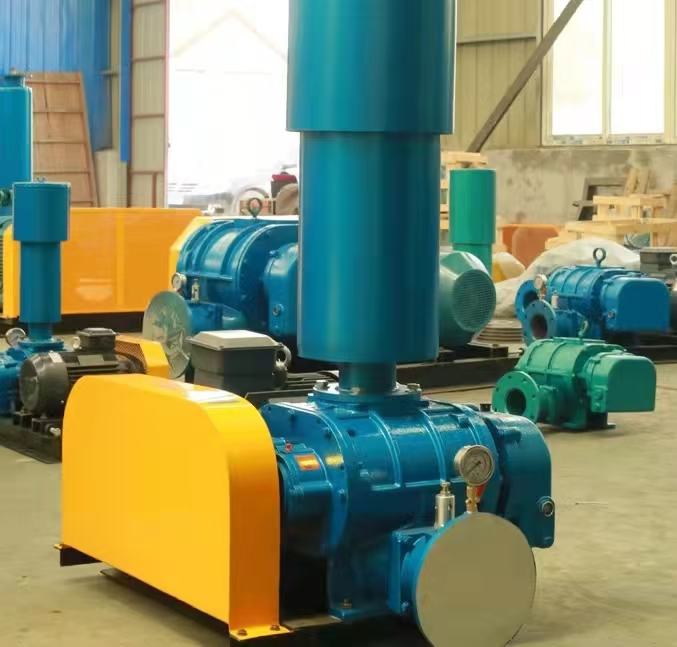
**1、 Analysis of Dust Sources in Boiler Systems**
|Dust type | Generation process | Particle size distribution | Typical concentration (mg/m3)|
|----------------|-------------------------|---------------|------------------|
|Coal powder * * | Coal fired boiler pulverizing system | 10-200 μ m | 50-500 μ m|
|* * Fly ash * * | Leakage of flue gas circulation/dust collector | 5-100 μ m | 20-200|
|Limestone powder | Flue gas desulfurization system (CFB boiler) | 1-50 μ m | 30-300|
|* * Metal oxides * * | Corrosion products of pipelines | 1-20 μ m | 5-50 μ m|
---
**2、 The harm of dust to Roots blower**
1. * * Mechanical damage**
-Blockage of rotor clearance (standard clearance 0.1-0.3mm) → efficiency decrease of 10-30
-Abnormal wear of bearings (reduced lifespan to 1/3 of normal value)
2. * * Performance impact**
-Filter blockage leads to an increase in intake resistance ↑ (for every 500Pa increase in resistance, energy consumption increases by 3-5)
-Dynamic balance failure of impeller → vibration value exceeding limit (ISO 10816 standard limit of 4.5mm/s)
3. * * Risk**
-Dust accumulation causes fire (ignition temperature of coal powder cloud: 430-500 ℃)
-Electrostatic discharge may ignite explosive mixtures (ignition energy<10mJ)
---
**3、 Technical Comparison of Dust Prevention Solutions**
|* * Scheme Type * * | * * Applicable Scenarios * * | * * Filtering Accuracy * * | * * Pressure Drop (Pa) * * | * * Maintenance Cycle * *|
|----------------|------------------------|--------------|--------------|--------------|
|* * Primary dust cover * * | Coarse particle pretreatment | ≥ 100 μ m | 50-80 | Weekly cleaning|
|Bag filter | Conventional coal-fired boiler | 5-10 μ m | 150-300 | Monthly blowback|
|* * Cyclone separator * * | High concentration dust (CFB boiler) | 20-50 μ m | 200-400 | Quarterly ash discharge|
|* * Wet scrubber * * | Viscous dust (flue gas after desulfurization) | 1-5 μ m | 500-800 | Daily drainage|
---
**4、 Recommended dust prevention system configuration**
**1. Typical Scheme of Coal fired Boiler**
```mermaid
flowchart LR
A [air inlet] -->B [louvered rain cover] -->C [cyclone pre separator] -->D [pulse back blowing bag filter] -->E [explosion-proof Roots blower]
```
**Key parameters * *:
-Filter air speed: ≤ 1.2m/min (anti bag damage)
-Anti static treatment: surface resistance<10 Ω
-Explosion proof requirement: Ex tD IIIB T130 ℃ (dust explosion-proof)
**2. Simplified Scheme for Gas Boiler**
-Just need stainless steel dust screen (mesh size 20-40)
-Pressure drop control: < 100Pa
---
**5、 Design Specification for Dust Prevention System**
1. * * Structural requirements**
-The effective flow area of the dust cover is ≥ 1.5 times the cross-sectional area of the fan inlet
-The inclination angle of the ash hopper is ≥ 60 ° (to prevent ash accumulation)
2. * * Material selection**
-High temperature zone (>120 ℃): 304 stainless steel wire mesh (φ 0.8mm)
-Corrosion environment: 316L stainless steel or PTFE coated filter material
3. * * Monitoring and Control**
-Differential pressure alarm set value:
-Bag filter: 1500Pa
-Primary filtration: 500Pa
-Interlock protection: Automatic start of blowback system when pressure difference exceeds the limit
---
**6、 Key points of maintenance management**
|* * Project * * | * * Standards * * | * * Tools/Methods * *|
|----------------|-------------------------|---------------------------|
|Filter material replacement | Resistance reaches twice the initial value | Differential pressure gauge monitoring|
|Impeller cleaning | Vibration value increases by more than 15 | High pressure water gun (pressure ≤ 50MPa)|
|Electrostatic detection | Quarterly surface resistance test | Megohmmeter (500V DC)|
|Protection | Nitrogen purge before shutdown maintenance | O content<5 before operation|
---
**7、 Economic Benefit Analysis**
**Case: Application of 75kW Roots blower in coal-fired power plants**
|* * Project * * | * * No Dust Prevention * * | * * Installing a Dust Prevention System * *|
|----------------|----------------------|-----------------------|
|Annual maintenance cost | ¥ 48000 (frequent replacement of bearings) | ¥ 12000|
|Energy consumption difference | Annual excess power consumption of 18000 kWh | Rated operating conditions|
|Equipment lifespan | 2-3 years | 5-8 years|
**Investment payback period * *: Dust prevention system cost ¥ 35000 → approximately 1.2 years to recover cost
---
**8、 Special working condition handling**
1. * * High humidity flue gas**
-Electric heating anti condensation (maintaining wall temperature>dew point 10 ℃)
-Automatic drainage of drain valve (flow rate ≥ 0.5L/min)
2. * * Flammable dust**
-Calculation of explosion vent area:
$$
A ≥ 0.034V^{2/3}
$$
(V - Equipment volume, m3)
-Explosion suppression system: CO injection response time<50ms
---
**Conclusion * *:
Roots blowers for boilers must be equipped with dust prevention systems, especially for solid fuel boilers such as coal-fired and biomass boilers. It is recommended to adopt the secondary filtration scheme of * * "cyclone separation+pulse cloth bag" * *, which can balance the filtration effect and operating resistance. For gas boilers, simple dust nets can meet the requirements, but regular inspections are needed to prevent insects and other foreign objects from entering.